Shipping labels are essential logistics ecosystem navigators, directing packages through intricate global networks.
Errors in shipping labels, such as incorrect addresses, inadequate packaging information, or regulatory non-compliance, can severely disrupt the delivery process. These disruptions often result in delays, increased costs, and lost shipments, impacting business operations and customer relationships.
This article delves into the prevalent mistakes made during shipping label preparation, analyses their consequences, and provides practical solutions.
Why Do Accurate Shipping Labels Matter?
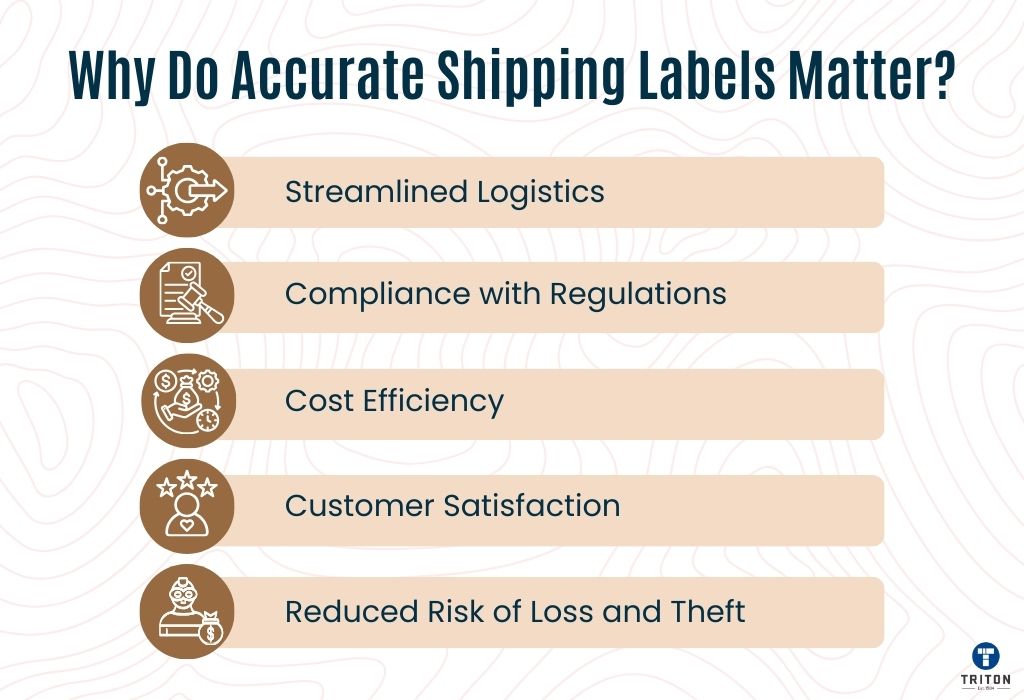
Accurate shipping labels are crucial for several reasons.
- Streamlined Logistics: Shipping labels contain all the essential information required for transporting, handling, and delivering packages. Accurate labels ensure that goods are routed correctly through complex logistics networks, reducing the chances of misdirection or delays.
- Compliance with Regulations: Many industries have specific regulations governing the shipping of goods, especially for hazardous materials like chemicals, international trade, or food products. Accurate labelling is necessary to comply with these regulations and avoid legal penalties or shipment rejections.
- Cost Efficiency: Errors in shipping labels can lead to additional costs such as return shipping fees, resending costs, and lost productivity. Accurate labels minimise these financial impacts by ensuring that shipments reach their correct destinations on the first attempt.
- Customer Satisfaction: Prompt and accurate delivery is crucial for maintaining customer trust and satisfaction. Mistakes in shipping labels can lead to delayed deliveries or lost packages, negatively impacting the customer experience.
- Reduced Risk of Loss and Theft: Proper labelling includes the address, tracking codes, and barcodes that help monitor the shipment’s progress. Accurate and complete labels reduce the risk of lost or stolen packages during transit.
Common Shipping Label Mistakes and How to Solve Them
This section delves into frequent shipping label mistakes, their repercussions, and practical solutions to mitigate them, ensuring a smoother delivery process.
Incorrect Printer Settings or Label Size
Utilising incorrect printer settings or an inappropriate shipping label size often results in labels that are misaligned or have crucial information cut off.
Such errors can lead to significant issues, including difficulties in barcode scanning, which is essential for tracking and processing shipments. Consequently, this increases the risk of packages being misdelivered or lost.
Prevention and Correction:
- Adjust Printer Settings: Before printing, ensure your printer settings are correctly configured for the type of label being used. This might involve selecting the ‘Label’ print mode or opting for similar settings that accommodate thicker paper, such as ‘Heavyweight’ or ‘Cardstock.’
- Choose the Right Label Size: Verify the label size requirements for your specific shipping carrier and service. Using carrier-provided templates can prevent size-related errors. If your labels are not fitting correctly, reassess the dimensions and select a size that matches the carrier’s standards.
- Conduct Pre-Printing Tests: Run a few test prints on regular paper to avoid wasting labels and time. This allows you to adjust alignment and settings without using your actual label stock.
Labels That Don't Adhere Properly
Labels might not stick effectively to packages due to several factors, such as substandard adhesive quality, surfaces that are not clean, or the use of label materials unsuitable for the package surface.
When labels detach during transit, the risk of packages becoming lost or undeliverable significantly increases. This can disrupt the delivery process and negatively impact customer satisfaction.
Prevention and Correction:
- Select High-Quality Labels: Opt for labels known for their superior adhesive qualities that are compatible with your packaging material, whether cardboard, plastic or any other substrate.
- Prepare the Surface: Clean the area where the label will be applied to remove dust, grease, or debris. The surface should be dry and flat to maximise adhesive contact.
- Choose Suitable Label Material: Ensure the label material is appropriate for the package’s surface texture and the expected environmental conditions, such as moisture or temperature changes.
Smudged or Blurry Labels
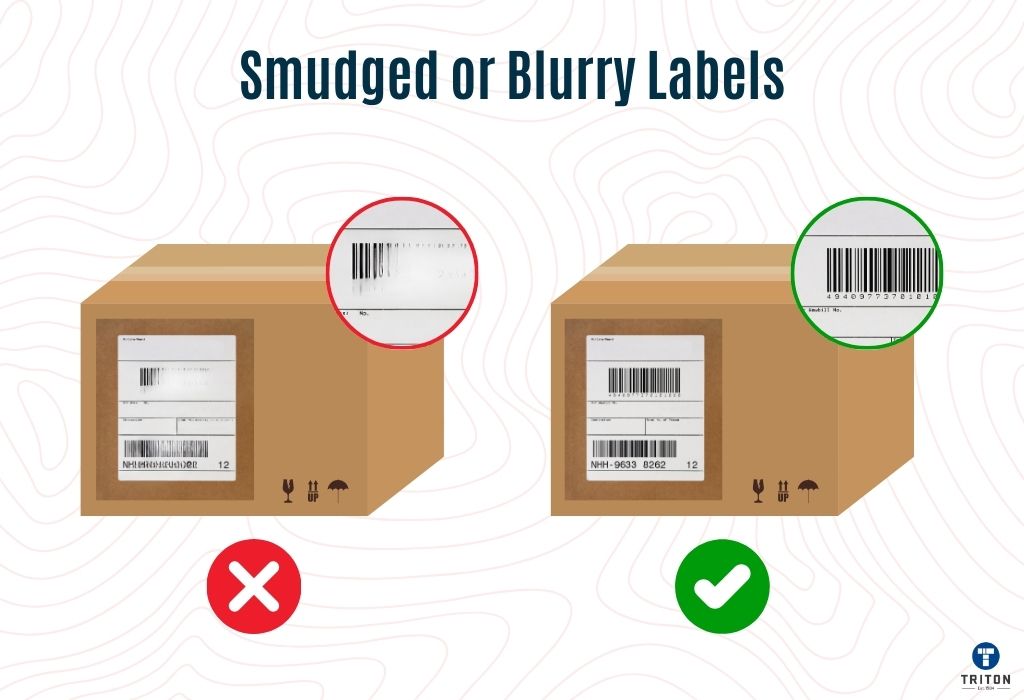
The use of thermal printers, ribbons, or labels that are incompatible with each other often results in shipping labels that are smudged or have blurry text and images.
This lack of clarity can significantly impede the readability of crucial label information and barcodes, essential for accurately tracking and processing shipments. As a result, packages may face delays during transit, affecting overall delivery efficiency.
Prevention and Correction:
- Match Printer Type and Labels: It is critical to match your labels with the appropriate printer type. Inkjet printers necessitate labels crafted to absorb liquid ink efficiently. In contrast, laser printers demand labels that endure the high temperatures needed to fuse toner to the surface. When using thermal printers, opt for thermal-specific labels that change colour upon exposure to heat, eliminating the need for ink or toner.
- High-Resolution Printing: Opt for your printer’s highest resolution settings to achieve precise and crisp printing results. This is particularly important for barcode legibility.
- Replace Incompatible Materials: If you encounter smudging or blurriness, assess the compatibility of your materials. Switch to labels specifically designed for your printer’s technology, and consider using manufacturer-recommended ink or toner.
Incorrect or Missing Information
The absence of essential details or the inclusion of erroneous information on shipping labels is a frequent oversight. This can encompass inaccuracies in addresses, weights, or improper service codes.
Such mistakes are prone to misrouting or delaying packages. In certain cases, carriers may also charge additional fees for corrections or rerouting.
Prevention and Correction:
- Accuracy Check: To ensure accuracy, carefully examine all data entries before printing labels. This includes double-checking addresses, package weight, and any applicable shipping codes or instructions.
- Carrier Address Validation Tools: Many shipping carriers and platforms offer tools to validate addresses against official postal service databases. Utilising these tools can help identify and rectify errors before labels are finalised.
- Correction Procedures: Contact the carrier immediately if a package is already in transit with incorrect or missing information. Many carriers can update shipping information mid-transit, though this may incur a fee.
Poor Label Placement
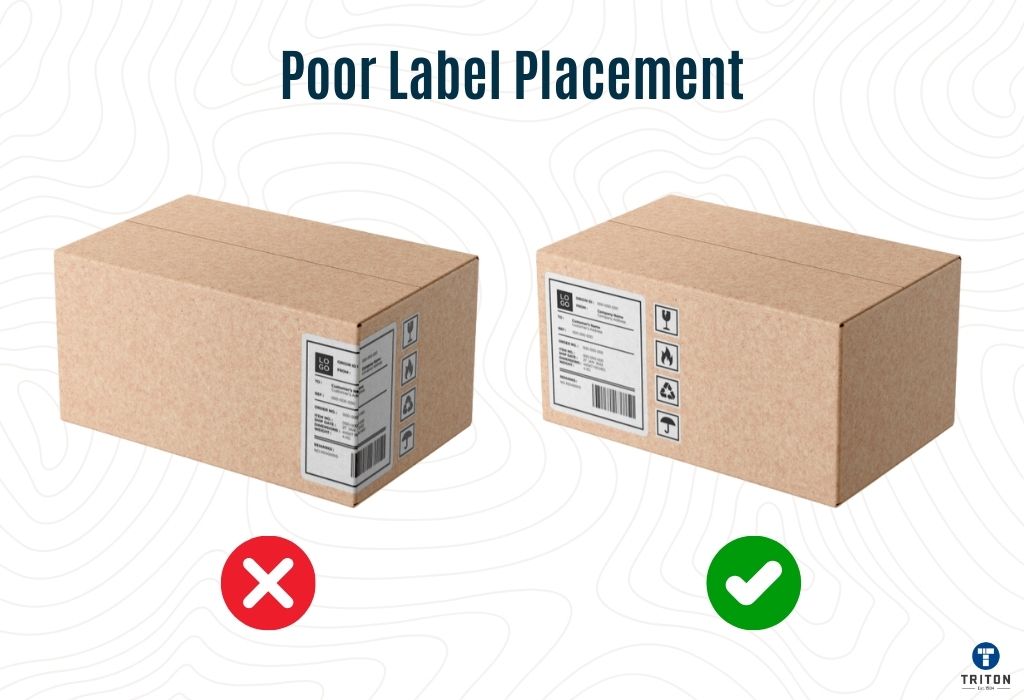
Inadequate placement of shipping labels, such as over package seams, edges, or irregular surfaces, can significantly impair label integrity and readability. It also causes difficulties in scanning barcodes, potentially causing delays and misdeliveries.
Prevention and Correction:
- Strategic Placement: Identify and utilise the largest flat area on the package for label application. This ensures maximum adhesion and visibility for scanning devices.
- Avoid Problematic Areas: Avoid placing labels over seams, edges, and corners of the packaging. These areas are prone to wear and compromise the label’s adherence and condition.
- Surface Preparation: Before label application, ensure the chosen spot is clean, dry, and free of any material that could undermine the label’s stickiness.
Inadequate Packaging for Weather Conditions
Neglecting to employ waterproof or weather-resistant labels for packages exposed to environmental elements like rain, snow, or high humidity can impair label integrity.
Exposure to such conditions renders labels unreadable, erasing crucial shipping information and barcodes. This compromises the ability to track and deliver packages accurately, potentially leading to lost shipments or significant delays.
Prevention and Correction:
- Use of Weather-Resistant Labels: Opt for labels that withstand harsh weather conditions. These labels are typically made from materials that repel water and resist tearing, ensuring information remains legible.
- Assessment of Shipping Conditions: Prior to shipping, evaluate the journey’s potential exposure to adverse weather. This foresight allows for selecting label materials best suited to the expected conditions.
- Supplementary Protection: In extreme conditions, consider additional protective measures, such as plastic sleeves or waterproof packaging, to safeguard the label and package integrity.
Colour and Print Quality Issues
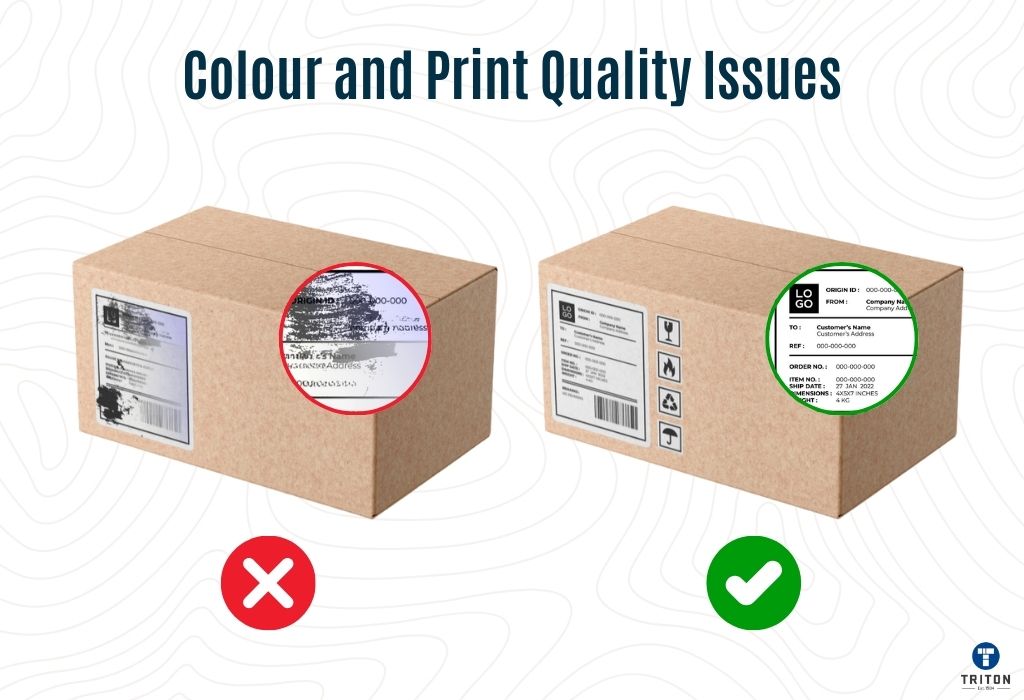
Variations in colour consistency and image resolution can disrupt the uniform appearance of shipping labels. This impacts both brand representation and the functional aspects of the label, such as barcode readability.
Prevention and Correction:
- Professional Printing Services: Consider using professional label printing software like BarTender or printing services for critical shipments, especially those representing your brand directly to customers. These services are equipped to maintain high colour accuracy and print quality standards.
- High-Quality Printing Equipment: If printing in-house, invest in high-quality thermal printers known for their precision in colour reproduction and ability to produce clear, high-resolution images. Regular maintenance of these printers is also crucial to ensure consistent performance.
- Standardised Colour Codes: Adhere to standardised colour codes like Pantone for branding elements to achieve uniform colouration across all printed materials, including shipping labels.
- Pre-Printing Checks: Before finalising a batch of prints, conduct tests to compare the output with your brand standards and adjust the printer settings if necessary. This step is vital for ensuring that the colours and resolution on the labels meet your requirements.
Not Accounting for International Shipping Requirements
International shipments necessitate adherence to specific labelling and customs documentation requirements that vary by destination. Overlooking these requirements can lead to significant complications in the shipping process.
Failure to comply with international labelling standards and customs documentation can result in shipments being held up at customs, incurring delays and potential returns or penalties. Such issues affect delivery timelines and can also lead to increased costs and customer satisfaction.
Prevention and Correction:
- Research Destination Regulations: Prior to shipping, it’s imperative to thoroughly research and understand the customs regulations and labelling requirements of the destination country. This includes any special labelling for hazardous materials, country-specific forms, and necessary customs declarations.
- Accurate and Complete Documentation: Ensure all required customs documents are accurately filled out and included with the shipment. This often involves detailed descriptions of the contents, their value, and the purpose of shipment.
- Use of International Shipping Platforms: Many shipping platforms and carriers offer tools and services designed to assist with international shipments. These tools can automatically provide the necessary forms and labels that comply with the destination country’s regulations.
- Continuous Learning: International shipping regulations can change, so staying updated on customs requirements or documentation changes is essential. Subscribing to updates from carriers or governmental trade resources can be beneficial.
Summing Up
In conclusion, the creation and application of shipping labels are critical components in the logistics and delivery process. Precision in label information, adherence to international requirements, and quality in label production are essential to avoid common pitfalls that can lead to delivery delays, increased costs, or customer dissatisfaction.
By implementing the strategies outlined for each common mistake, businesses can ensure a smoother delivery process and maintain the integrity of their supply chain.
We hope this article has provided valuable insights into optimising shipping label practices for your logistics needs.
Thanks for reading!
Frequently Asked Questions
What Happens if a Shipping Label Is Incorrect?
When a shipping label contains incorrect details, the package is misrouted, experiences delays, or is returned to the sender. Additional fees for correcting or rerouting the shipment by the carrier might apply.
Contacting the shipping carrier immediately to rectify any inaccuracies on the label and minimise potential disruptions is essential.
Is Folding a Shipping Label Acceptable?
Folding a shipping label is discouraged as it can affect the label’s readability, particularly the barcode, leading to scanning difficulties. Ideally, labels should be affixed to a flat, smooth package area.
If folding is unavoidable due to the package size, care should be taken to ensure the barcode is on a single, uninterrupted surface.
How Can I Ensure My Shipping Label Is Water-Resistant?
It is important to use labels specifically designed to be waterproof or water-resistant to ensure a shipping label is sufficiently resistant to water.
An alternative method is to cover the label with clear waterproof tape or place it inside a plastic sleeve for protection. However, it is important not to cover the barcode with tape that creates glare, as this can impede scanning.
Can a Shipping Label Be Reused for a Different Package?
No, a shipping label can not be reused for a different package. Each label is unique, containing specific information and tracking numbers intended for the original package.