Store Location
Choose Your Store
You are currently in the New Zealand store. If you are located in Australia please select the correct store below.
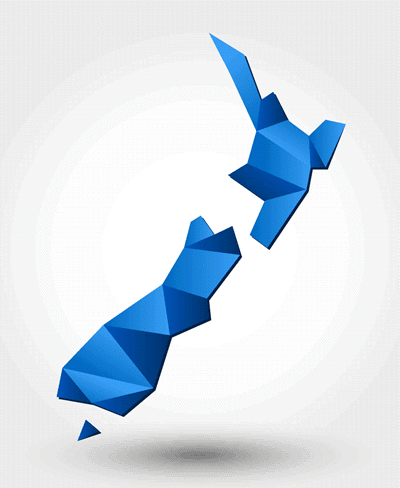
You are currently in the New Zealand store. If you are located in Australia please select the correct store below.
Checkweighing systems are an integral part of packing and manufacturing businesses. From food production process to pharmaceuticals, these systems help ensure that products are correctly portioned and weighed. By automating the process of check weighing, companies can improve accuracy and efficiency while reducing costs.
Triton offers a range of checkweighing solutions. From simple, entry-level systems to more sophisticated in motion scales, we have a checkweighing system to suit every business need.
Our selection of checkweighing systems provides businesses with an affordable, accurate, and reliable way to weigh products. With features like multi-language support, touchscreen displays, and USB connectivity, our checkweighing systems are sure to provide superior performance.
Contact us via the live chat widget below to learn more about our checkweighing solutions.
Checkweighers are an automatic or manual machine that weighs, classifies, and segregates items by weight. They are sometimes used in combination with metal detectors or x-ray inspection systems to inspect products for metal contaminants or other foreign objects.
Checkweighers are available in different shapes, sizes, and configurations to meet the needs of different production lines. They are commonly used in food processing, pharmaceuticals, and packaging applications to ensure that each product meets the specified weight conditions.
“Checkweigher” and “Checkweighing System” are often used interchangeably. However, they are not the same thing.
A checkweigher is the physical scale that does the actual weighing of products on a conveyor belt.
A checkweighing system, on the other hand, is a complete solution that includes the checkweigher, software, and integration with other systems like metal detectors, x-ray inspection machines, or vision inspection systems.
Checkweighing systems occupy a larger footprint than checkweighers and are more expensive. However, they offer higher accuracy and automation, making them the preferred choice for most industrial applications.
At Triton, we offer both standalone checkweighers and complete checkweighing systems.
There are numerous reasons why checkweighing is essential in industrial applications. Some of the most important reasons are listed below.
Most industries are regulated by governmental agencies like the FSANZ, FDA, USDA, or DOT. These agencies have strict product labelling guidelines that compel businesses to mention the exact weights and measures of the products on the label.
Checkweighers help businesses meet labelling guidelines by ensuring that each product is accurately weighed and labelled before it is shipped. This protects businesses from penalties and fines and prevents product recalls that damage a company’s reputation.
For example, Australian trade measurement legislation clearly states that no pre-packaged goods can have a shortfall greater than 5% of the advertised quantity. This law means if a product is supposed to weigh 100 grams, the actual weight of the product cannot be less than 95 grams. If it does, the business will be liable to pay penalties.
Product weight is one of the main factors that determine shipping costs. Inaccurate weights cause businesses to overpay for shipping, resulting in significant financial losses.
Checkweighers help businesses get accurate product weights, which helps estimate shipping costs accurately and avoid overspending. The weight information is also used to optimize packaging and choose the most economical shipping method.
Products like fruits, vegetables, meat, flour, and spices are often sold by weight. These products have a short shelf life, and businesses must ensure they sell the right quantities.
Checkweighers helps businesses keep track of inventory by accurately weighing each batch of products. This weight information can be used to optimize production schedules, adjust prices, and order the right quantities of raw materials.
Checkweighers are used as an effective quality assurance system. By weighing each product, manufacturers can identify underweight or overweight items.
If an item is underweight, it indicates that the product is not meeting the required specifications. This can be due to defective packaging, missing product items (like cords and manuals), or incorrect portion sizes.
If an item is overweight, it indicates that the product may contain foreign objects (like metal shards or glass), is overfilled, or has thick packaging.
In both cases, the product is considered defective and should never reach the end user.
Checkweighers can be set up to reject or isolate underweight or overweight products before they are shipped out. Additionally, checkweighers can be integrated with metal detectors, x-ray inspection machines, or vision inspection systems, further increasing the accuracy of product quality control.
Did You Know?
According to Food Standards Australia New Zealand, foreign particles were the fourth most common cause of food recall in 2021.
Checkweighers maintain a record of the weight of each product that passes through them. This data can be used to track production trends, optimize production processes, optimize marketing strategies, and troubleshoot issues in the manufacturing process.
Checkwighers are available in a variety of configurations to suit different applications. Here are some of the most common types of checkweighers.
Static checkweighers are scales designed to measure the weight of products that are not in motion. They are used to spot-check the weight generally for sampling purposes.
Static checkweighers require an operator who manually places the product on the scale platform for weighing. The weight is then displayed on a digital readout for the operator to record. The operator then decides if the product meets the specifications or not.
Static checkweighers are best suited for applications where a small number of products need to be checked for weight accuracy, like in quality control or research and development.
Static checkweighers are also known as manual checkweighers, check scales, and over/under scales.
Dynamic checkweighers weigh products while they are in motion on a conveyor belt. They are used in high-speed production lines where a large number of products need to be weighed quickly and accurately.
Dynamic checkweighers are automated and do not require an operator. The product’s weight is measured as it passes over the scale platform. If the product falls outside the acceptable weight range, it is rejected and removed from the conveyor belt.
Dynamic checkweighers are best suited for applications where a large number of products need to be checked for weight accuracy, like in food production or pharmaceutical manufacturing.
Dynamic checkweighers are also known as in-motion checkweighers, conveyor checkweighers, in-line scales, and belt weighers.
Heavy-weight checkweighers are designed to weigh heavy products, like pallets of bottled drinks, aquatic animals, or sacks of flour. They are used in applications where the weight of the product is expected to be more than 25 kilograms.
Heavy-weight checkweighers have a large-scale platform that can accommodate heavy products. They have a slow belt speed ranging between 5 to 60 meters per minute.
Combi-check checkweighers are dynamic checkweighers that are integrated with a metal detector or x-ray inspection machine. These checkweighers check the weight and the presence of metal contaminants or other foreign objects simultaneously.
The metal detector or x-ray machine is placed above the conveyor belt before the checkweigher platform. If a foreign object is detected, the machine stops the conveyor belt and triggers an alarm horn with an LED light. The product is then manually removed from the conveyor belt. Automated rejection systems and rejection lines can also be used rather than a manual process.
Combi-check checkweighers are best suited for applications where products need to be checked for weight accuracy and foreign contaminants, like in the food or pharmaceutical industries.
Sorting checkweighers are dynamic checkweighers that direct products to different production lines or chutes based on weight.
Sorting checkweighers have a conveyor belt with multiple product chutes branching off of it. As the products pass over the scale platform, they are weighed and routed to the appropriate chute corresponding to their weight range.
Sorting checkweighers are also known as weight-classifying machines.
Weigh price labelling machine’s are dynamic checkweighers that integrates a labelling machine. These checkweighers weigh the product, calculate the price (based on the weight), and print and apply the label with the weight and price information in one process.
See Triton’s other product pages for both automatic weigh price labelling and manual carton weigh labelling
A static checkweigher is a simple machine that features a scale platform and a weighing terminal. The product is placed on the scale platform, and the weight is displayed on the weighing terminal.
On the other hand, a dynamic checkweigher is a more complex machine that features various conveyor belts.
A typical checkweighing system comprises the following components.
The infeed belt is the first conveyor belt in the machine. It is used to bring the product to the scale platform. The speed of the infeed belt can be adjusted to speed up or slow down the flow of products.
The weighing belt is the second conveyor belt in the machine. This is where the product is weighed. The weighing belt contains load cell sensors that measure the product’s weight. Load cells are transducers that convert a physical force, like weight, into a measurable electrical signal. Once the products are weighed, they are routed to the outfeed or reject belt.
The outfeed or reject belt is the last conveyor belt in the machine. This belt sort the product based on their weight. The products that meet the desired weight range are allowed to pass through, while those that do not meet the desired weight range are rejected and routed to a separate chute. The outfeed or reject belt has automated removal devices like pneumatic pusher arms or air jets that help sort the product.
The weighing terminal is the user interface of the machine. It is used to set the desired weight range, view the weight, and alter the machine settings.
Checkweighing systems are used in a variety of industries for different purposes. Some of the most common uses of checkweighing systems are listed below.
Check weigh systems are designed and built to withstand tough industrial environments. However, there are always things that should be done to extend the life of this type of equipment.
Here are a few tips to protect your check weigh system.
A checkweigher system serves a variety of industries. Some of the most common industries that use checkweighers are.
Ideally, a checkweigher system should be installed at the end of a production line, just before the product is packaged.
If there are rejcetions or auto sorting based on weight then this can be further up the production stream.
If you don’t follow governmental regulations and industry standards, you can potentially face regulatory and legal action. You may be subject to.
Linearity is the ability of a checkweigher to show the actual weight of a package throughout the entire weighing range. It is tested by putting known weights on balance ranging from near zero to full capacity.
The more linear a checkweigher is, the more accurate it will be in weighing packages of different weights.
Repeatability refers to the ability of a checkweigher to show the same weight for a given product when weighed multiple times. It is tested by weighing a known weight numerous times and seeing how close the results are to each other.
The more repeatable a checkweigher is, the more accurate it will be in weighing packages of different weights.
Accuracy is the measurement of the uncertainty in the results provided by the checkweigher. It measures how close the checkweigher will get to the true value of the measured weight.
The more accurate a checkweigher is, the more confident you can be in its ability to weigh products accurately.
The accuracy of a checkweigher can be affected by many factors, including.
Error is the difference between the actual weight of a package and the weight shown by the checkweigher. It can either be positive, negative or zero.
A positive error means that the checkweigher reading is higher than the true value.
A negative error means that the checkweigher reading is lower than the true value.
A zero error means that the checkweigher reading is the same as the actual value.
Auckland
Christchurch
Phone 09 579 2057
Live Chat – Widget below
Auckland
Christchurch
Phone 09 579 2057
Live Chat – Widget below