When it comes to thermal printing technology, there are two main methods: direct thermal and thermal transfer.
Direct thermal and thermal transfer both have their own pros and cons that should be considered when deciding which method to use. But what exactly are these printing methods? Are there any differences or similarities between the two? And the most important question is; which one should you use?
To help you with that decision, we’ve put together a comprehensive guide on direct thermal and thermal transfer printing.
We will start by explaining direct thermal and thermal transfer printing with its pros and cons. We will then compare both printing methods head to head. Finally, we will provide tips on factors that should be considered when choosing a printing method.
So, without further ado, let’s get started!
What is Direct Thermal Printing?
Direct thermal printing is a type of printing where heat from the thermal printhead is used to produce images using heat-sensitive paper.
The heat-sensitive paper has ink embedded in it. Therefore, when the paper passes under the thermal printhead, the heat from the printhead activates the ink and turns the paper black. The heat-sensitive paper then rapidly cools down and sets the image before it exits the printer.
As the thermal printhead comes in direct contact with the print media (paper), this type of printing process is named direct thermal printing.
Direct thermal printers are simple to use and maintain. They do not require ribbons or inks, making them a cost-effective printing solution. In addition, direct thermal printers are smaller and lighter in weight, making them portable. Most mobile & desktop printers use direct thermal printing technology.
However, because the printhead makes direct contact with the paper, printhead damage due to friction is a common issue with direct thermal printers. Also, if any debris or foreign material is present on the paper, it can cause burns and permanent damage to the printhead.
As the label material is heat sensitive, the print quality of direct thermal labels degrades over time. The labels start to fade and become unreadable after a certain period (usually 6 to 9 months). Moreover, the images printed using direct thermal printing are not resistant to smudging, scratching, or exposure to direct sunlight, chemicals, and water.
Direct thermal printing is best suited for short-term applications where label durability is not a concern. Some common examples include.
- Boarding passes
- Receipts
- Event tickets
- Coupons & discount codes/coupons
- Name tags
- Baggage tags
- Retail label printing
- Shipping & dispatch labels
- Short-lived shelf items like food labels
Pros and Cons of Direct Thermal Technology
Pros and Cons | |
---|---|
Pros
| Cons
|
No ink, toner, or ribbon to monitor or replenish
| Limited lifespan of labels
|
Cheaper than thermal transfer
| Labels are not resistant to harsh weather conditions, chemicals, or abrasions
|
Easy media changeovers
| Prints black ink only
|
More durable than dot matrix or laser printers print jobs.
| May require regular printhead replacement
|
Creates virtually no waste
|
What is Thermal Transfer Printing?
Thermal transfer printing is a type of printing where heat from the thermal printhead is used to transfer dye from a ribbon onto the print media (paper, label, etc.).
A ribbon is a thin film coated with wax, resin, or a combination of both on one side. The ribbons sit between the printhead and the print media. So, when the ribbon passes under the thermal printhead, the heat from the printhead melts the wax or resin. This, in turn, releases the dye, which is then transferred onto the paper. The dye cools down and sets on the paper, creating a high-quality image.
As the dye is transferred from the ribbon to the paper, this type of printing process is named thermal transfer printing.
Thermal transfer printers are known for their high-quality prints and durability. They can produce labels resistant to smudging, scratching, and exposure to strong sunlight, chemicals, and water.
However, because of their complexity, a thermal transfer printer is typically more expensive than a direct thermal printer. Thermal transfer printers also require more maintenance as they have more moving parts.
Thermal transfer printers are usually rugged and heavy, which makes them difficult to transport. Industrial printers typically use thermal transfer printing technology.
Thermal transfer printing is best suited for long-term applications where label durability is a concern. Some common examples include.
- Barcode printing
- Asset tags
- Product/inventory identification labels
- Cold storage and freezer labels
- Laboratory specimen labeling
- Blood bag labeling
- Warehouse shelf labels
Pros and Cons of Thermal Transfer Technology
Pros and Cons | |
---|---|
Pros | Cons |
High print quality compared to direct thermal printing
| Requires thermal ribbons
|
Long lifespan of labels
| Expensive than direct thermal printing
|
Thermal transfer labels are resistant to harsh weather conditions and abrasion
| Can be wasteful if single-pass thermal transfer ribbon is used and very little is printing on it
|
Can print colored labels
| Needs more maintenance
|
Long printhead life
|
Thermal Transfer VS Direct Thermal
Thermal transfer and direct thermal printing do have some similarities like they both use heat to print images. However, they also have some essential differences that make each printing process unique and ideal for different applications.
Now that we have a better understanding of each printing method let’s compare direct thermal printing and thermal transfer printing side by side.
Direct Thermal VS Thermal Transfer | ||
---|---|---|
Direct Thermal
| Thermal Transfer
| |
Print Quality
| Good quality
| High-quality
|
Print Readability and Scanability
| Good readability and scannability
| Maximum readability and scannability
|
Print Shelf Life
| Between 6 to 9 months
| Easily last more than a year
|
Resistant to Harsh Environmental Conditions and Abrasion
| No | Yes |
Printer Materials and Supplies Required
| Heat-sensitive media
| Thermal transfer ribbons
|
Color Printing
| No; only black ink
| Yes; requires colored ribbons
|
Print head Life
| Direct contact with the media (and debris) which cause friction, causing permanent damage.
| No direct contact with print media. Print head comes in contact with ribbon that has a special back coating that reduces friction.
|
Cost | Cost-effective
| Costly |
Environmental Aspect
| No wastage
| Can cause waste if a single pass ribbon is used
|
General Application
| Receipt, shipping labels, tickets,
| Product identification labels, barcode labels,
asset tags, product tags
|
Factors to Consider While Choosing a Printing Method
Now that we have compared direct thermal printing and thermal transfer printing, it’s time to choose a printing method that is best suited for your needs. Here are some factors you should consider while making your decision.
Preferred Lifespan of the Labels
The first and most important question you need to answer is how long you need your labels to last.
Direct thermal printed labels last for a short time, whereas thermal transfer printed labels have a longer lifespan.
Type of Environment
Another factor you need to consider is the environment in which the printed labels will be used.
If your printed labels are exposed to harsh environmental conditions like strong sunlight, extreme temperatures, or exposure to water and moisture, then you should opt for thermal transfer printing. Otherwise, direct thermal printing would be sufficient.
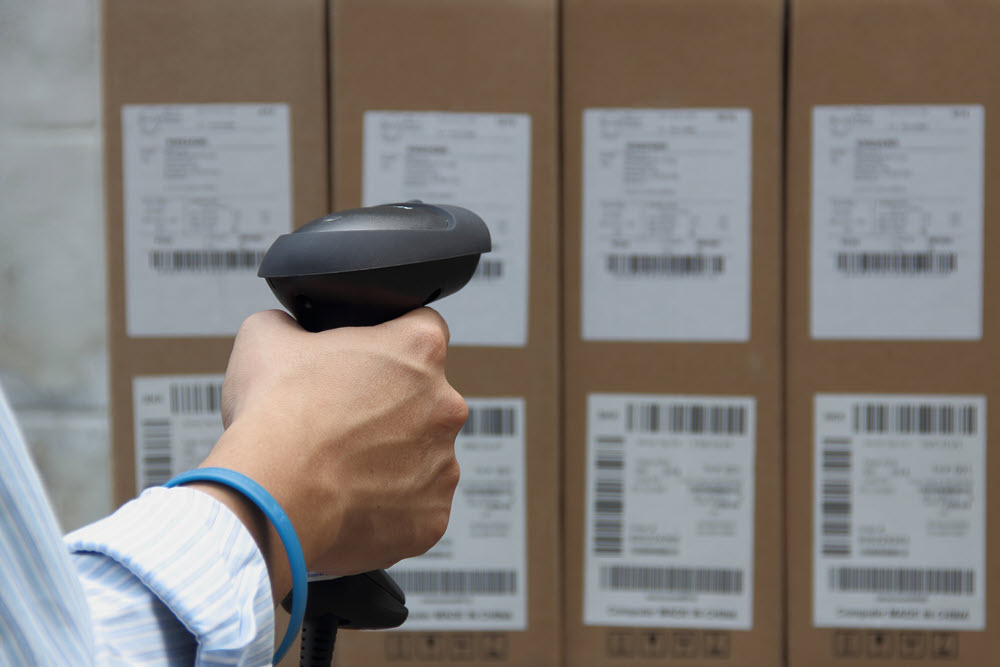
Exposure to Chemicals or Similar Substances
You must also consider whether your printed labels will be exposed to chemicals or substances.
If the answer is yes, then thermal transfer printing is the way to go. Otherwise, direct thermal printing would suffice.
Print Quality
When it comes to print quality, both direct thermal and thermal transfer printing can produce quality prints. But, as a direct thermal printer uses only heat to print images, the quality of direct thermal prints is often not as good as thermal transfer prints.
So, if you need high-quality prints with sharp and crisp texts and images, then thermal transfer printing would be the better option.
Cost
The last factor you need to consider is the cost of the printing method.
Ribbons are required for thermal transfer printing and can be pretty expensive in the long run. Additionally, thermal transfer printers are typically more expensive than direct thermal printers.
So, if you are working on a tight budget, then direct thermal printing would be the best choice for you.
Final Verdict
As you can see, there are both advantages and disadvantages to each type of printing method. Ultimately, the best type for you will depend on your specific needs and requirements.
To summarize, direct thermal printing is best suited for short-term applications where label durability is not a concern. On the other hand, thermal transfer printing is ideal for long-term applications where label durability is essential.
We hope this article has helped you understand the difference between direct thermal and thermal transfer printing. If you have any questions, please feel free to reach out to us via the live chat widget below. Our experts would be more than happy to assist you.
Choosing a thermal printer can be a challenge, but our guide on the 7 best thermal printers will help you make an informed choice.
Happy printing!