Dot peen marking (also known as pin marking or pin stamping) is a flexible and low cost method of permanently indenting parts with text, serial numbers, logos, or data codes using a rapidly striking pin.
In this article, we’ll explore how dot peen marking works, its different types, and its key benefits, giving you a clear understanding of this effective marking method.
How does Dot Peen Marking work?
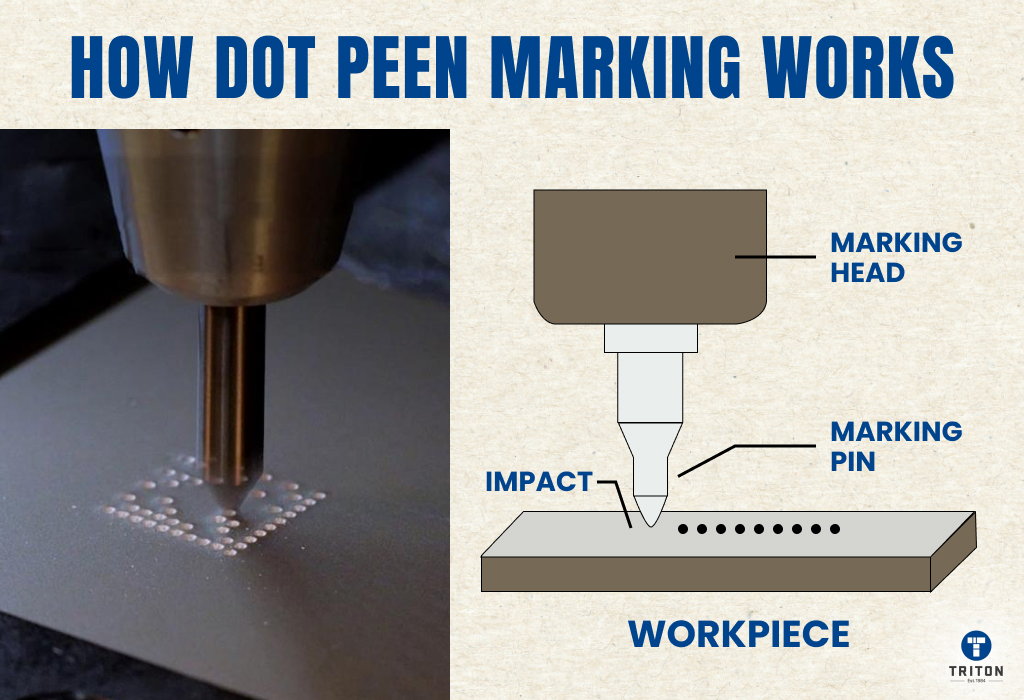
At its core, dot peen marking works by striking a material’s surface with a pointed stylus, creating a series of indentations that form the desired marking. Each impact produces a single dot, and by controlling the x-y position of successive dots, the system can “draw” alphanumeric characters, logos, or even 2D barcodes like Data Matrix codes.
The marks are made via material displacement rather than material removal – the stylus plastically deforms the substrate, pushing it downward to create a dot. This means no chips or dust are created; the process is akin to miniature cold forging of each dot.
Dot peen marking is considered a low-stress process since it only indents the surface and does not significantly compromise the part’s fatigue strength (a key reason it’s approved for aerospace and pressure-containing parts).
The frequency of pin strikes is very high. Electromechanical pins can cycle at hundreds of hertz. For example, industrial multi-pin systems can mark on the order of a dozen or more characters per second.
The exact speed depends on factors like the number of pins, character size, and material hardness, but dot peen is generally faster than manual stamping and can approach the throughput of some laser systems for typical text marking tasks.
System Components and Design
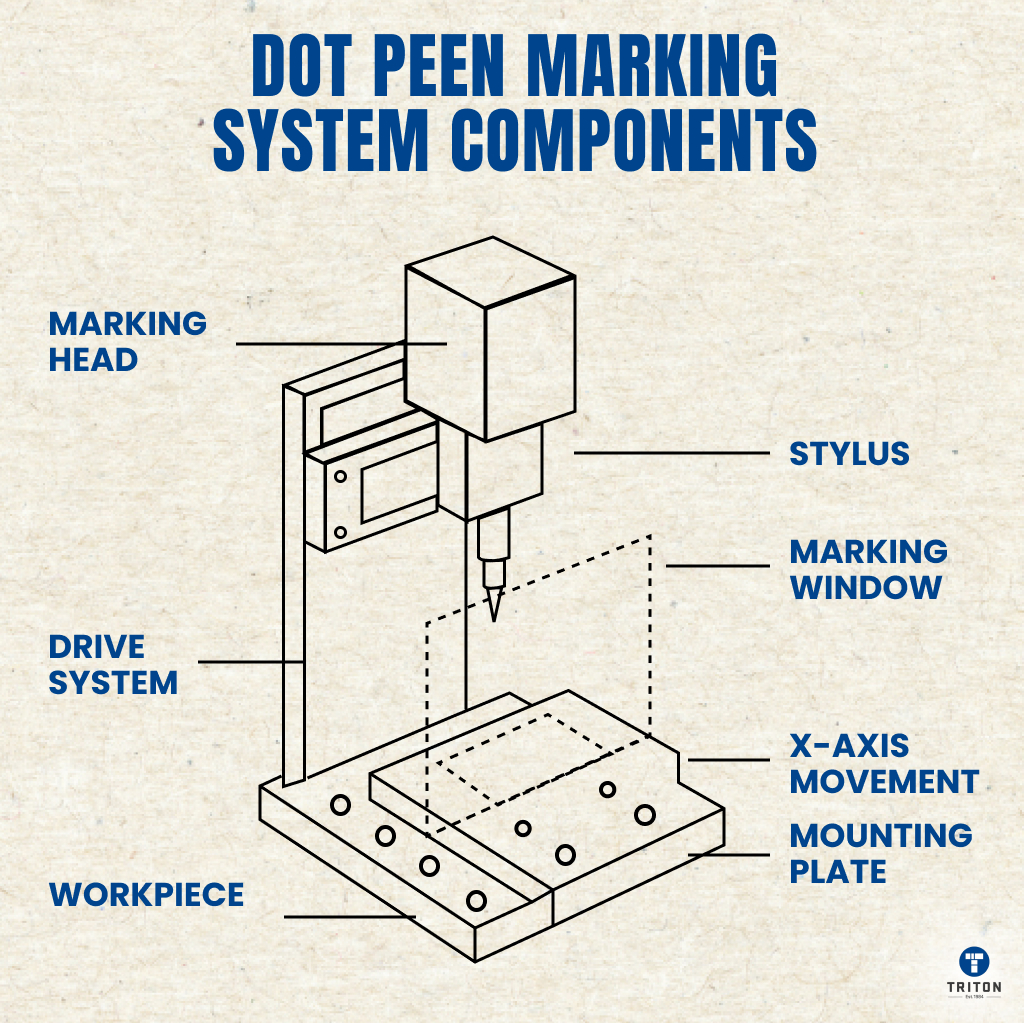
A dot peen marking system consists of five key components:
- Marking Head and Stylus: The stylus is housed inside the marking head and driven by either a solenoid (electromechanical) or an air piston (pneumatic). It is made from tungsten carbide or diamond, and is usually conical (around 90°). Some heads include floating mounts or auto-sensing features to keep depth consistent on uneven surfaces.
- X–Y Positioning Stage: The stylus moves over the part (marking area) using two linear axes, defining the marking window. The marking window is typically 160 × 100 mm for benchtop units and about 50 × 30 mm for handheld models. High precision stepper or servo motors move the stylus over the marking window.
- Controller Unit: The controller stores marking data, triggers pin strikes, and coordinates movement. It can be a standalone box or PC-based software, with support for USB, Ethernet, serial, and I/O connections. Advanced markers include wireless control, touchscreens, and inline code verification using cameras.
- Frame and Fixturing: The machine’s frame holds the marking head in position. Benchtop models use a vertical column; portable units have ergonomic housings. Fixtures, clamps, or standoffs are used to steady the workpiece and ensure accurate marking.
- Power and Pneumatics: Electromechanical systems run on standard mains power. Pneumatic systems need compressed air at 4–6 bar. Marking force is adjusted by regulating air pressure or current, depending on the actuation method.
Together, these components automate the dot peen process—delivering fast, durable, and repeatable marks with minimal operator input.
Electromechanical vs. Pneumatic Systems
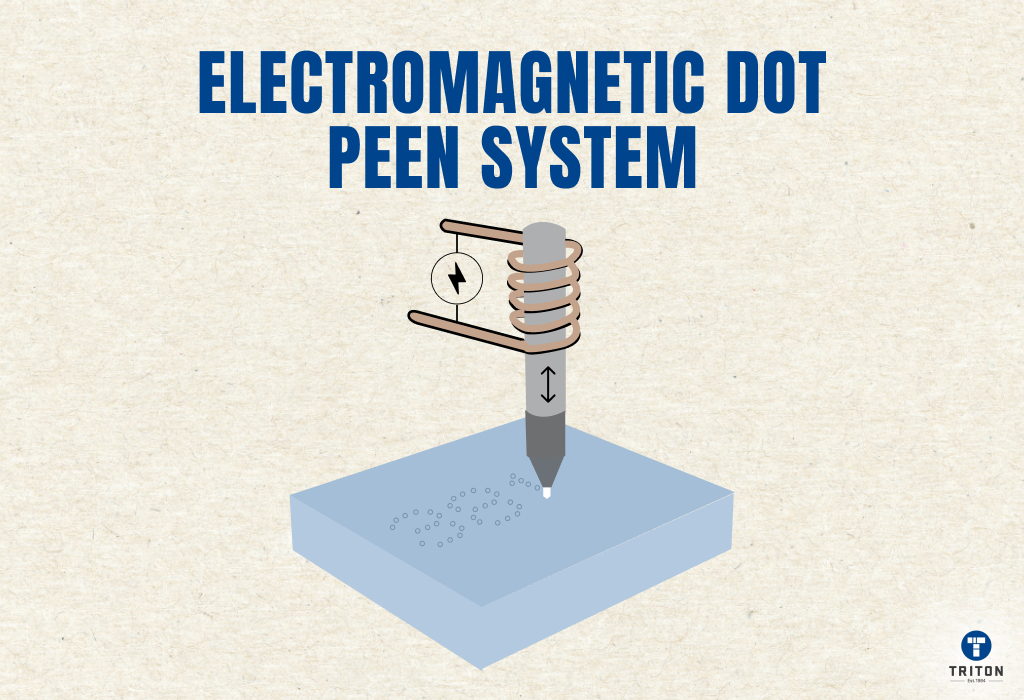
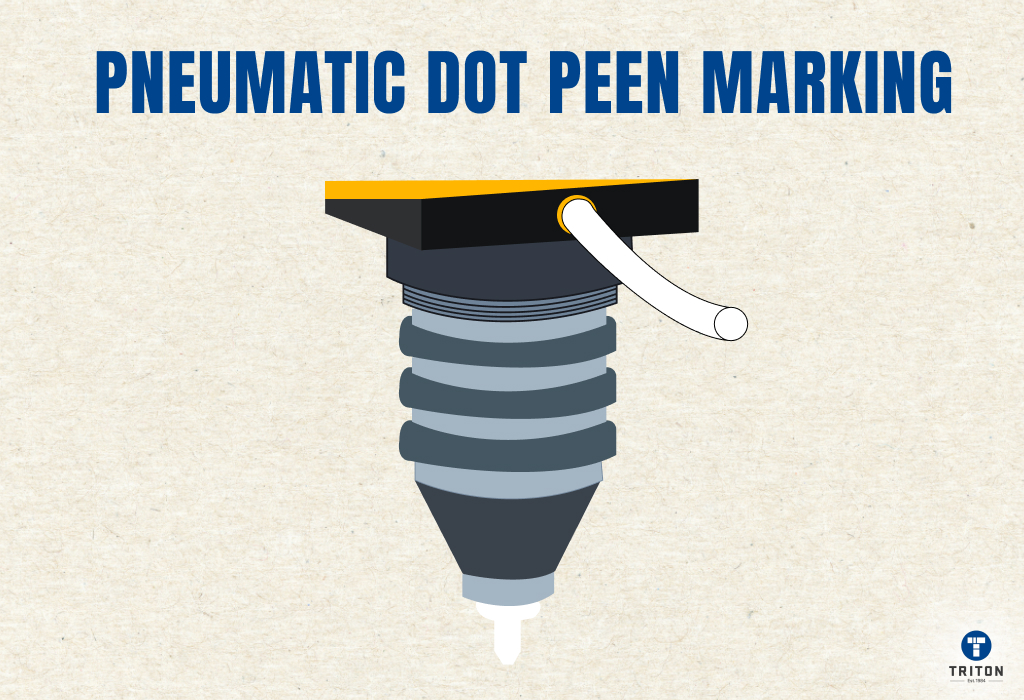
Dot peen machines generally use one of two methods to drive the stylus: electromagnetic (electromechanical) actuation or pneumatic actuation. Both achieve the same result (a rapidly reciprocating pin) but have different characteristics:
Electromechanical systems use a solenoid or similar electromagnetic driver to propel the stylus forward, and a spring or secondary coil for retracting it. These fully electric systems require only a power connection. Electromechanical designs are simple to install and are low maintenance.
Although historically slower than pneumatic systems, modern electromechanical markers now achieve comparable speeds, and multi-pin configurations can mark up to 16 characters per second.
Pneumatic systems use compressed air to drive the stylus. These systems have very high impact frequencies, and create deep & heavy marks quickly.
Pneumatic units excel in high-throughput settings, for instance, stamping VINs on steel chassis or marking thick metal tags.
Air pressure adjustments directly influence the marking force, with typical operating pressures around 4 to 6 bars. Some designs feature a floating pin to better adapt to uneven surfaces.
On the downside, pneumatic dot peen marking systems depend on clean and stable air supply. Fluctuations in pressure affect mark depth and quality. They also require regular maintenance to keep air dry and filters clear, and they are louder due to air exhaust.
Both systems yield excellent, durable marks. The choice between electromechanical and pneumatic actuation depends on desired precision, available infrastructure, marking depth, speed requirements, and maintenance preferences.
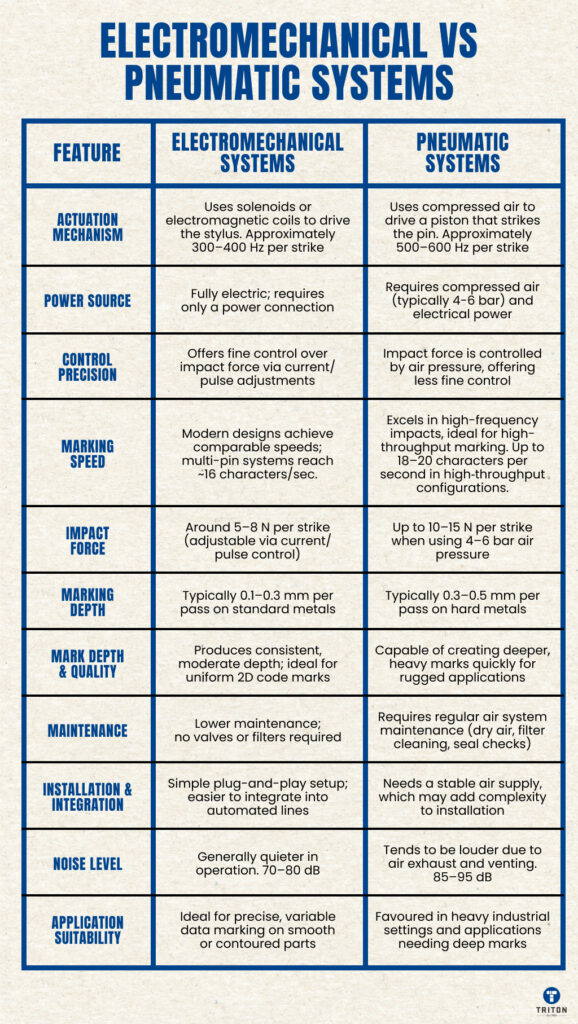
Feature | Electromechanical Systems | Pneumatic Systems |
---|---|---|
Actuation Mechanism | Uses solenoids or electromagnetic coils to drive the stylus. Approximately 300–400 Hz per strike | Uses compressed air to drive a piston that strikes the pin. Approximately 500–600 Hz per strike. |
Power Source | Fully electric; requires only a power connection. | Requires compressed air (typically 4-6 bar) and electrical power. |
Control Precision | Offers fine control over impact force via current/pulse adjustments. | Impact force is controlled by air pressure, offering less fine control. |
Marking Speed | Modern designs achieve comparable speeds; multi-pin systems reach ~16 characters/sec. | Excels in high-frequency impacts, ideal for high-throughput marking. Up to 18–20 characters per second in high‑throughput configurations. |
Impact Force | Around 5–8 N per strike (adjustable via current/pulse control). | Up to 10–15 N per strike when using 4–6 bar air pressure. |
Marking Depth | Typically 0.1–0.3 mm per pass on standard metals. | Typically 0.3–0.5 mm per pass on hard metals. |
Mark Depth & Quality | Produces consistent, moderate depth; ideal for uniform 2D code marks. | Capable of creating deeper, heavy marks quickly for rugged applications. |
Maintenance | Lower maintenance; no valves or filters required. | Requires regular air system maintenance (dry air, filter cleaning, seal checks). |
Installation & Integration | Simple plug-and-play setup; easier to integrate into automated lines. | Needs a stable air supply, which may add complexity to installation. |
Noise Level | Generally quieter in operation. 70–80 dB | Tends to be louder due to air exhaust and venting. 85–95 dB. |
Application Suitability | Ideal for precise, variable data marking on smooth or contoured parts. | Favoured in heavy industrial settings and applications needing deep marks. |
Stylus Tip Geometry and Marking Parameters
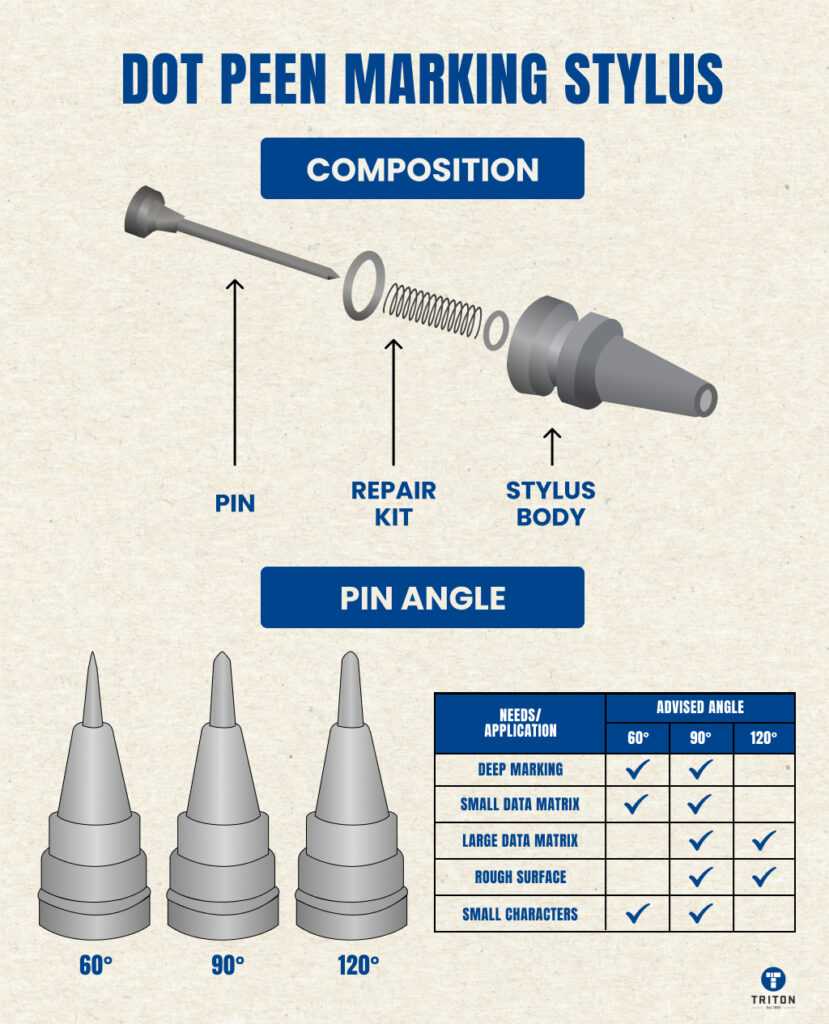
Most styluses feature a conical point, with a standard included angle of about 90°. However, manufacturers offer a range from approximately 60° to 120° to suit different applications. The choice of tip angle is a balance between mark depth, dot size, and stylus durability.
A smaller tip angle, such as 60°, concentrates the force on a smaller area. This results in deeper penetration for a given impact force – tests have shown that on aluminum, a 60° tip can achieve ~0.28 mm depth in one pass. The deeper indentation is beneficial for marking on very hard materials; however, the trade-off is that the pin becomes prone to faster wear or chipping, and the resulting dots are narrower. This reduction in dot diameter compromises the visual contrast and readability of text or barcodes.
Conversely, a larger tip angle like 120° spreads the impact force over a wider area, producing shallower but broader dots. Although the mark depth is reduced, the increased dot diameter enhances contrast, making the marks easier to read. This is especially important for 2D codes where consistent, larger dots improve the scanning reliability.
A blunter tip is physically stronger, has a longer operational life with less frequent chipping, even on hard materials. A 120° tip provides a more robust and legible mark when high-density code patterns are needed.
A 90° tip serves as a compromise between depth and dot size. This angle produces moderate indentation and durability. Many systems are pre-configured with 90° carbide tips because they handle a broad range of applications effectively. Some dot peen systems have multiple tips. For instance, a user might select a 60° tip for achieving deep marks on soft steel or switch to a 120° tip for high-density barcodes on aluminum surfaces.
Tip Angle | Mark Characteristics | Trade-offs |
---|---|---|
60° | Deep indentation (~0.28 mm on aluminium); narrow dots | Higher force concentration; increased wear/chipping; reduced contrast |
90° | Moderate depth and dot size | Balanced performance; widely used for general applications |
120° | Shallower but broader dots; enhanced dot contrast | Lower depth per strike; improved durability and readability |
Additional Marking Parameters
In addition to tip geometry, other marking parameters significantly affect the outcome. Impact frequency, marking force, and traverse speed are adjustable through the machine’s software.
Increasing the impact frequency can speed up the marking process; however, if the force per strike is insufficient, the dots become too shallow. Operators can compensate by slowing the traverse speed or applying multiple passes to achieve the desired depth. The stand-off distance – typically maintained between 2 to 5 mm – is also critical.
This gap allows the stylus to gain momentum, with a larger gap sometimes yielding deeper marks until a limit is reached. Lastly, character size and font design, such as a “5×7” dot matrix configuration, influence overall mark clarity. Choosing the right combination of these factors is essential for balancing depth, clarity, and cycle time.
Parameter | Typical Range | Consequences |
---|---|---|
Impact Frequency | 300–600 Hz | Faster strikes speed up marking; too high with low force yields shallow dots. |
Marking Force | 5–15 N | Sufficient force deepens marks; too little makes faint dots, too much may damage the surface. |
Traverse Speed | 1–100 mm/s | Slower movement results in deeper, clearer marks; high speeds risk reduced dot depth. |
Stand-off Distance | 2–5 mm | Proper gap builds momentum for optimal impact; deviations cause inconsistent mark depth. |
Character Size & Font | 1–50 mm | Small fonts (<3 mm) risk poor readability; larger fonts improve clarity but require more marking space. |
Types of Dot Peen Marking Machines

Portable Dot Peen Marking Machines
Portable dot peen markers are made for marking large or fixed parts on-site.
They weigh a few kilos and often run on rechargeable batteries. The operator holds the unit by hand and presses it against the surface to mark. This setup works well for tasks like VIN marking on truck chassis, marking pipes, or tagging heavy castings.
Despite their size, many models can mark hard materials – up to 62 HRC – and run for hours on a single charge.
Some units have built-in touchscreens or keypads so users can enter data directly. Others support wireless connections to load marking files.
Most portable markers have small marking windows – typically between 50×20 mm and 100×30 mm. This keeps the unit light and rigid. LEDs or laser pointers are often included to help line up the mark.
Portable systems suit field work and low-volume jobs. For high-throughput marking, fixed systems are still the better option.
Benchtop Dot Peen Marking Machines
Benchtop dot peen systems are fixed machines used in workshops or production areas. The marking head is mounted on a Z-axis column above a flat worktable. This setup helps with accurate and repeatable marking.
These machines usually have larger marking windows – around 160×100 mm – and adjustable columns with a travel range of 200-300 mm. That lets operators mark parts of different sizes.
Their solid frames and stable fixtures help produce clean, consistent marks, even on hard metals. Parts are often clamped in place using vises, fixtures or rotary devices.
Benchtop systems are common in production lines. Many are fitted with automatic tag feeders or linked to assembly stations. They are reliable, fast, and well-suited to marking identification tags, small parts or metal components with little operator input.
Integrated and CNC-Mounted Systems
Integrated dot peen systems are built to work with automated equipment. These machines include a compact marking head and a separate control unit. They are installed on conveyors, robot arms or CNC machines.
In some setups, the marking head sits over a conveyor and marks each part as it passes by. Standard I/O signals connect the marker to the rest of the production line for easy control.
CNC-mounted versions go straight into machining centres. Some tools attach to the spindle, turning the CNC machine into a combined machining and marking station. That means no need to move the part to a second machine.
These systems are used in high-volume manufacturing. Automotive plants, for example, use them to mark engine parts with Data Matrix codes. Cameras then check the marks automatically. These setups focus on speed and uptime.
Specialised Configurations
Some dot peen machines are built for special jobs.
Deep-marking units are often pneumatic. They make deep marks – over 0.5 mm – on forged or heavy parts like steel bars. These marks stay visible even after painting or coating.
Tag marking machines are benchtop units with feeders. They can quickly process large batches of ID tags.
Some machines can switch between portable and benchtop modes. These are useful in shops that handle a wide range of parts and job types.
Suitable Materials, Marking Depth, and Hardness Limits
Dot peen marking is a versatile process that works on a wide range of materials. It marks most metals including steel, stainless steel, aluminum, brass, copper, and titanium – and many hard plastics.
Even some ceramics or composites can be marked if they are not too brittle. Since dot peen relies on mechanical impact, material hardness is the primary limiting factor. In general, commercial machines can mark materials up to 60-65 HRC, with ~62 HRC as a practical upper limit.
Beyond this, such as with extremely hard tool steels or carbide, the tungsten carbide stylus skids or barely scratches the surface, wears quickly, or even chips. In these cases, laser marking or engraving is the better option.
For the vast majority of industrial alloys below 62 HRC, dot peening creates clear, permanent marks. For instance, structural steel (around 20 HRC) and aluminum (<10 HRC) are easy to mark and yield deep, crisp dots. Hardened die steel (~55 HRC) is near the upper limit but remains markable with a sharp pin at slower speeds. Common automotive and aerospace alloys, treated steels, and cast irons fall within this range as well. Even softer materials like plastic, wood, or leather can be marked, although dot peen is an overkill for such substrates.
Marking depth depends on both the material and machine settings. On soft metals like aluminum, marks can exceed 0.3 mm deep and may reach ~0.5 mm or more with a double pass.
In contrast, on harder steel, pneumatic systems are used and can mark 0.15–0.38 mm deep dots. In cold-rolled steel (~RB53) with a 60° pin, versus ~0.55 mm in aluminum under the same conditions.
Typical single-pass depths for dot peen on steel are around 0.1-0.3 mm. Deep marking machines, such as Gravotech’s XF530, can reach ~0.5 mm in one pass, a much needed depth for parts subject to abrasive wear or sandblasting.
Parameter | Range/Value | Details |
---|---|---|
Materials | Most metals, hard plastics, some ceramics & composites | Works on steel, stainless steel, aluminum, brass, copper, titanium; also marks ceramics/composites if not too brittle. |
Hardness Limit | ~60–65 HRC (practical limit ~62 HRC) | Beyond this, the tungsten carbide stylus may skid, barely scratch, wear quickly, or chip; alternative methods (e.g. laser marking) are recommended for extremely hard tool steels or carbides. |
Marking Depth (Soft Metals) | >0.3 mm; up to ~0.5 mm (with multiple passes) | On materials like aluminum (<10 HRC), deep, crisp marks are achievable; multiple hits can further deepen the mark. |
Marking Depth (Hard Metals) | ~0.1–0.3 mm (single-pass); ~0.15–0.38 mm (cold-rolled steel, ~RB53) | Structural steel (~20 HRC) and hardened die steel (~55 HRC) yield shallower marks; deep marking machines (e.g. Gravotech XF530) can reach >0.5 mm in one pass. |
Extreme Hardness | ~0.01–0.05 mm | Marking materials at 60+ HRC produces very shallow dents (small dots/pinpricks); a diamond stylus may improve penetration, or other methods might be used. |
Surface Tolerance | N/A | Capable of marking through mill scale, oxides, paint, or dirt; effective on surfaces with roughness (Ra) up to 10 µm without pre-cleaning, making it ideal for castings and forgings with inherent surface irregularities. |
Enhanced Depth Control | Dynamic (variation <0.01 mm) | Advanced systems incorporate sensor feedback to adjust marking depth in real time, ensuring uniform marks across surfaces with minor hardness variations—a key advantage in aerospace and automotive applications.
|
Temperature Impact | +5–10% depth increase at ~50°C | Material temperature affects dot depth; parts pre-heated to around 50°C may yield marks that are 5–10% deeper compared to room temperature, important in processes where parts are already warm.
|
Multi-Pass Strategies | 3 passes can yield ~0.5 mm on hardened steel (~55 HRC) | While a single pass typically produces 0.2–0.3 mm depth, multiple passes cumulatively achieve deeper marks, enhancing durability on parts subject to abrasive wear or sandblasting. |
Innovative Stylus Materials | Diamond-coated or composite tips | These advanced tips offer improved wear resistance, extending the stylus life cycle by up to 150% compared to standard carbide tips, especially when marking extremely hard materials. |
Use Cases and Industry Applications
Dot peen marking is widely used for permanent identification across industries.
In the automotive sector, it marks VINs, engine blocks, and other components with serial numbers and barcodes. In aerospace and defense, it provides low-stress marking for flight-critical parts and military equipment.
Heavy industries like oil, gas, and construction use dot peen to mark pipes, valves, and structural parts, while tooling and metalworking applications include marking dies, molds, and small components.
In logistics and packaging, durable identification is applied to containers, pallets, and equipment, ensuring traceability and compliance even under harsh conditions. It remains a reliable, cost-effective solution.
Industry | Applications | Key Advantages |
---|---|---|
Automotive | VINs, engine blocks, serial numbers, barcodes | Deep, permanent marks; resistant to corrosion and repainting; ideal for high-volume, automated production. |
Aerospace & Defense | Flight-critical parts, turbine blades, fasteners, military equipment | Low-stress marking preserves material integrity; compliant with standards (e.g., ATA SPEC2000, MIL-130); endures extreme conditions.
|
Oil & Gas / Heavy Machinery | Pipes, valves, fittings, structural parts, steel beams | Marks large, heavy parts in situ; effective on rough surfaces; withstands harsh environments. |
Tooling & Metalworking | Dies, molds, tools, gauges, industrial gears, small components | Customizable, programmable identification; ideal for quality control and inventory management.
|
Logistics & Packaging | Metal containers, pallets, asset IDs on equipment | Durable marks that resist outdoor exposure and cleaning; essential for long-term traceability and compliance. |
Medical Devices | Surgical instruments, implantable components, hospital equipment | Permanent, low-stress marks that withstand sterilisation; critical for traceability and quality assurance. |
Rail & Transportation | Rail components, train car parts, safety-critical assemblies | Highly durable in harsh, outdoor environments; ensures long-term traceability and regulatory compliance.
|
Renewable Energy | Wind turbine components, solar panel frames, energy equipment | Marking that endures extreme weather and mechanical stress; supports maintenance and lifecycle tracking in energy applications.
|
Marine Applications | Ship parts, offshore platform components, marine hardware | Resistant to corrosion and saltwater exposure; provides durable identification for maintenance and safety tracking in maritime settings. |
Consumer Electronics | Metal parts in devices, serial numbers on high-value components | Tamper-proof, permanent identification; ensures longevity and reliability in high-tech, service-critical components. |
Advantages and Limitations
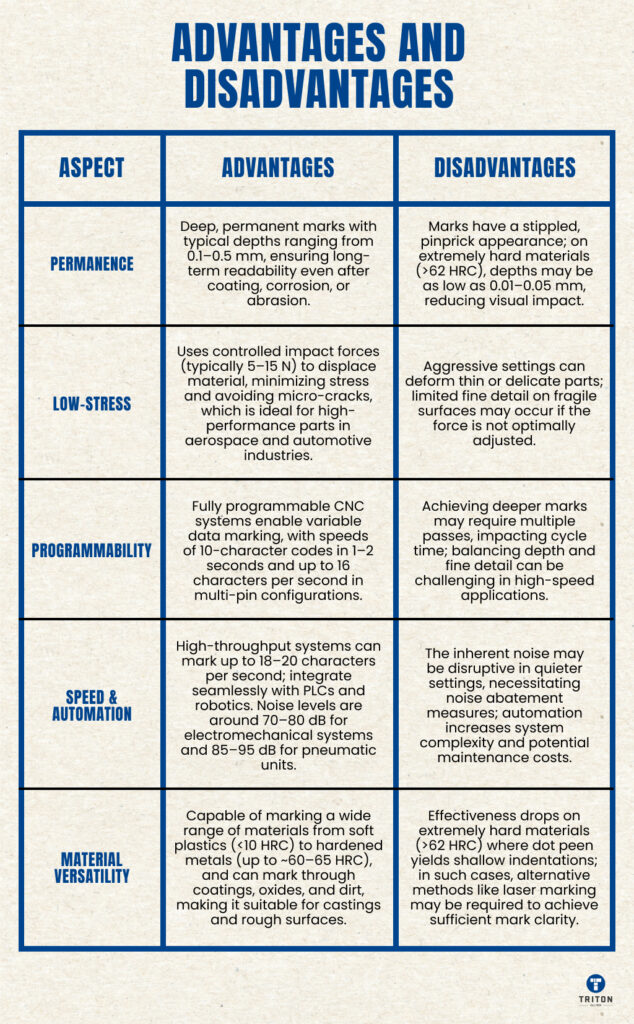
Dot peen marking provides permanent, durable identification by creating deep, hard-wearing indentations on various materials. It is low-stress, preserving part integrity and suitable for high-performance applications across automotive, aerospace, heavy machinery, and more. Its programmability allows variable data and quick changeovers, while automated systems enable high-speed, cost-effective production.
However, dot peen marks exhibit a stippled appearance, lower contrast, and the process is noisy. They deform thin or delicate surfaces, and detail is limited compared to laser marking. Trade-offs exist between depth and fine detail, often requiring multiple passes or post-processing to enhance mark readability. Overall, dot peen marking excels.
Aspect | Advantages | Limitations |
---|---|---|
Permanence | Deep, permanent marks with typical depths ranging from 0.1–0.5 mm, ensuring long-term readability even after coating, corrosion, or abrasion. | Marks have a stippled, pinprick appearance; on extremely hard materials (>62 HRC), depths may be as low as 0.01–0.05 mm, reducing visual impact. |
Low-Stress | Uses controlled impact forces (typically 5–15 N) to displace material, minimizing stress and avoiding micro-cracks, which is ideal for high-performance parts in aerospace and automotive industries. | Aggressive settings can deform thin or delicate parts; limited fine detail on fragile surfaces may occur if the force is not optimally adjusted. |
Programmability | Fully programmable CNC systems enable variable data marking, with speeds of 10-character codes in 1–2 seconds and up to 16 characters per second in multi-pin configurations. | Achieving deeper marks may require multiple passes, impacting cycle time; balancing depth and fine detail can be challenging in high-speed applications. |
Speed & Automation | High-throughput systems can mark up to 18–20 characters per second; integrate seamlessly with PLCs and robotics. Noise levels are around 70–80 dB for electromechanical systems and 85–95 dB for pneumatic units. | The inherent noise may be disruptive in quieter settings, necessitating noise abatement measures; automation increases system complexity and potential maintenance costs. |
Material Versatility | Capable of marking a wide range of materials from soft plastics (<10 HRC) to hardened metals (up to ~60–65 HRC), and can mark through coatings, oxides, and dirt, making it suitable for castings and rough surfaces. | Effectiveness drops on extremely hard materials (>62 HRC) where dot peen yields shallow indentations; in such cases, alternative methods like laser marking may be required to achieve sufficient mark clarity. |
Comparison with Other Marking Technologies
Method | Permanence | Cost | Speed | Surface Prep | Material Limits |
---|---|---|---|---|---|
Dot Peen | High | Medium | Medium | Low | Metals, Plastics |
Laser Marking | Very High | High | Fast | Clean surface | Limited by reflectivity |
Inkjet Marking | Low | Low | Fast | Clean surface | Mostly flat surfaces |
Engraving | Very High | High | Slow | Medium | Metals, Wood |
Dot peen marking is a reliable way to mark parts permanently. It works well across many industries and produces clear, tamper-resistant marks that support traceability and help meet compliance needs.
The system is programmable, cost-effective, and handles a wide range of materials. While it’s not ideal for delicate surfaces and can be noisy, its overall performance makes it a strong choice for manufacturers.
Triton supplies quality dot peen and printing systems for businesses with different marking needs. Visit the Triton Store to explore tools that support efficient, consistent production.