Effective product tracking and management are critical problems. Barcodes stand as a solution, enabling accurate tracking of products from production through to end-use across primary, secondary, and tertiary packaging levels.
This article systematically unpacks the barcode system, illustrating how it operates at each packaging level to streamline the supply chain. It aims to equip readers with a clear understanding of barcodes’ pivotal role in enhancing supply chain efficiency and accuracy by offering a detailed examination.
What are the Levels of Packaging?
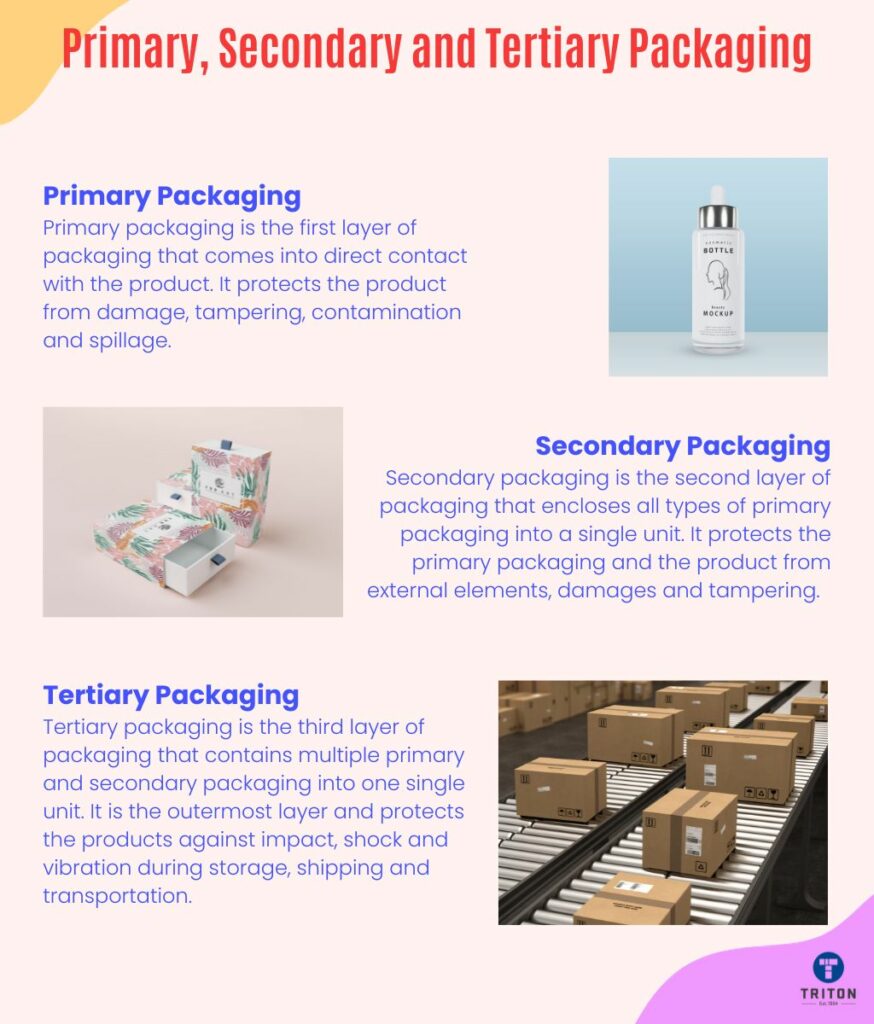
Packaging is an essential component in the shipping and retail industry that ensures product safety, integrity, and transportability. It is systematically organised into three primary levels: primary, secondary, and tertiary packaging.
Primary Packaging
Primary packaging is the product’s first layer of protection. It is in direct contact with the product itself and serves multiple purposes. Primarily, it safeguards the product against contamination, damage, and degradation. It also provides consumers critical information such as barcodes, QR codes, ingredients, usage instructions, and expiration dates.
Secondary Packaging
Secondary packaging consolidates one or more units of primary packaging for easier handling and distribution. It provides additional protection during storage and transit, ensuring the primary packages remain intact and products are not damaged.
Secondary packaging is often where branding and product information are more prominently featured for retail display purposes.
Tertiary Packaging
Tertiary packaging is designed for bulk handling, storage, and transportation and is typically not seen by consumers. Its main purpose is to facilitate the efficient handling, storage, and transport of large quantities of goods, often combining multiple secondary packages into one unit.
Barcodes for Different Levels of Packaging
Barcodes are the fundamental link between physical products and digital information systems in modern logistics and retail operations. These standardised identifiers enable automated tracking, inventory management, asset tracking and efficient processing at various supply chain stages.
Given the hierarchical packaging structure, different types of barcodes are utilised for primary, secondary, and tertiary packaging.
Barcodes for Primary Packaging
Primary packaging barcodes directly facilitate consumer transactions and product identification at the retail level. The most common types used are the Global Trade Item Number (GTIN) variants: GTIN-12 (Universal Product Code or UPC) in North America and GTIN-13 (International Article Number or EAN) in other parts of the world.
Before we proceed further, let us take a quick glance at the various types of barcodes we’ve talked about here.
GTIN-12 (UPC)
The GTIN-12, commonly known as the Universal Product Code, is a 12-digit barcode standard widely used in North America. It’s primarily found on primary packaging and is essential for retail point-of-sale (POS) scanning.
UPC barcodes are used on individual consumer goods like food items, apparel, and electronics, facilitating easy price lookup and inventory management in retail settings.
GTIN-13 (EAN-13)
The GTIN-13, known as the International Article Number, is a 13-digit barcode standard used outside of North America. It serves a similar purpose to the GTIN-12, accommodating retail products for international distribution.
GTIN-14
The GTIN-14 encodes information about the contained products in secondary and tertiary packaging levels. It’s designed for cases, cartons, and pallets that are not typically scanned at retail POS systems but are crucial for inventory and shipment tracking.
This barcode is applied to larger units that group multiple items for shipping or storage, facilitating the management of bulk quantities through the supply chain.
GS1 DataMatrix
The GS1 DataMatrix is a two-dimensional (2D) barcode that can encode vast information in a small space. It is used when space is at a premium and additional data, such as batch numbers and expiration dates, are required.
The GS1 DataMatrix barcode is common in healthcare and pharmaceutical industries.
Barcodes for Secondary Packaging
Secondary packaging barcodes facilitate the management of multiple primary packages as a single unit during handling, storage, and transportation. The ITF-14 barcode is a common choice, representing the GTIN of the contained product and enabling tracking cases or cartons through distribution centres and warehouses.
ITF-14 barcodes are designed for scanning on conveyor belts and in logistics environments where quick, reliable reading is essential. EAN/UPC barcodes are employed to facilitate POS scanning for secondary packages that also have a retail purpose, such as multi-packs that can be sold intact.
For a detailed comparison and understanding of the differences between EAN and UPC barcodes, please see our in-depth article: UPC vs EAN.
Barcodes for Tertiary Packaging
Tertiary packaging barcodes are critical for logistics and bulk transportation. They are used on pallets, crates, and large containers to facilitate warehouse management, logistics planning, and the movement of goods across the supply chain.
The GS1-128 barcode is frequently employed at this level. It is capable of encoding extensive information such as batch numbers, shipment IDs, and expiration dates. GS1-128 barcodes support Serial Shipping Container Codes (SSCC) that uniquely identify each shipping unit, allowing for the tracking and tracing of goods from the manufacturer to the final distribution point.
Overview of GTIN Packaging Labels
To effectively manage and identify product packages at various levels, the Global Trade Item Number (GTIN) system classifies packaging into distinct categories. Each category reflects the hierarchy and complexity of packaging logistics, ensuring accurate tracking and distribution across different supply chain stages.
Packaging Level | Description | Example |
---|---|---|
Each | The lowest level of the item hierarchy intended or labelled for individual sale is assigned a GTIN-12 (UPC). | A single chocolate bar labelled for retail.
|
Inner Pack
| Intermediate package of multiples of the same trade item or a predefined assortment, representing a single GTIN.
| A box of 10 chocolate bars, sold as one unit.
|
Case | A standard shipping unit that contains “eaches” of the same GTIN, packaged either individually or grouped as an inner pack.
| A case containing 6 boxes of chocolate bars.
|
Mixed Case
| Contains more than one type of “each,” must have more than one GTIN, and can include eaches or inner packs.
| A case with different types of candies, each packaged separately.
|
Pallet | A shipping unit containing either case, inner packs, or eaches, with one GTIN regardless of item grouping. | A pallet loaded with cases of various beverages.
|
Mixed Pallet
| Contains any combination of cases, inner packs, and/or eaches, and must have more than one GTIN.
| A pallet mixed with cases of soda and boxes of snacks. |
Display Shipper
| A self-contained display shipping unit can include a single type of “each” or multiple types.
| A promotional display containing several types of beverages.
|
Case as Each
| Used for goods shipped as a case, contents inside are neither assigned GTINs nor sold individually.
| A large appliance shipped in its case sold as a single unit.
|
Summing Up
This article has explored the critical role of barcodes at various packaging levels within the supply chain, highlighting how they enhance tracking, management, and efficiency from the manufacturing floor to the end consumer. We’ve detailed the specific types of barcodes used for primary, secondary, and tertiary packaging, each tailored to meet the unique demands of different packaging levels.
Barcodes such as GTIN-12 and GTIN-13 are indispensable at retail, facilitating smooth point-of-sale transactions and inventory management. At the distribution and logistics level, barcodes like ITF-14 and GS1-128 play a pivotal role in streamlining operations, enabling bulk handling and detailed tracking of shipments. These systems ensure that every packaged item, whether a small consumer good or a large shipping unit, is accurately monitored throughout its journey in the supply chain.
We hope this article was helpful.
Thanks for reading!