A DPM, short for Direct Part Marking barcode, is a permanent, machine-readable code applied to a product using techniques like laser etching, dot peening, or inkjet printing to facilitate tracking and identification of an asset throughout its lifecycle.
In this article, we will delve into the world of Direct Part Marking barcodes, exploring their significance in various industries. We’ll uncover the methods used to create these enduring codes, their role in enhancing tracking and identification processes, and their numerous benefits to businesses.
Whether you’re new to DPM barcodes or seeking to expand your knowledge, join us as we unravel the intricacies of this transformative technology.
Check out our barcode learning centre to learn all about today’s barcoding technology.
Purpose of Using DPM Barcodes
DPM barcodes serve a multifaceted purpose in the world of product management and traceability. These permanent markings play a crucial role in tracking each individual part throughout its entire lifecycle, commencing from production and extending to deployment and even the end consumer’s hands.
One of the primary advantages of DPM is its ability to ensure continuous traceability. This starts from the moment an item rolls off the manufacturing line, guaranteeing that every step in its journey can be meticulously monitored.
Here’s how DPM serves various critical functions:
- Enhanced Supply Chain Management: DPM facilitates the seamless tracking of parts within complex supply chains. Providing a clear digital trail helps avert misplacements and mix-ups, thereby optimising logistical operations.
- Post-Deployment Utility: Even after a product reaches its final destination – the end consumer – the etched DPM code continues to serve a purpose. It allows for potential future checks, facilitates hassle-free returns, and supports maintenance tasks, contributing to an extended and efficient product lifecycle.
What is the Difference Between DPM Barcodes and Regular Barcodes?
DPM barcodes and traditional barcodes serve a similar fundamental purpose: to store information in a format that barcode scanning devices can quickly and accurately read. However, the methodology and application behind these two types of barcodes are distinctly different, catering to varied use cases and industries.
Unlike traditional barcodes, which are typically printed on labels and then adhered to products, DPM barcodes are directly etched, engraved, or otherwise marked onto the item’s material itself. This ensures that the barcode becomes an integral and virtually inseparable part of the item, eliminating the risk of being removed or damaged during handling, transportation, or usage.
The direct marking technique employed in DPM is particularly advantageous for items where applying a conventional label is impractical or where the barcode needs to be resilient against harsh conditions, such as extreme temperatures, corrosive environments, or situations involving rigorous handling.
Refer to the following guides to learn more about barcoding technology.
- Barcode 101 – a beginner-friendly guide on barcodes
- Barcode types – an explanation of different barcode symbologies
- Discrete vs continuous barcodes – a comparison guide on 1D barcodes
- 2D stacked barcodes vs 2D matrix barcodes – a comparison on 2D barcodes
Benefits of Using DPM Barcodes
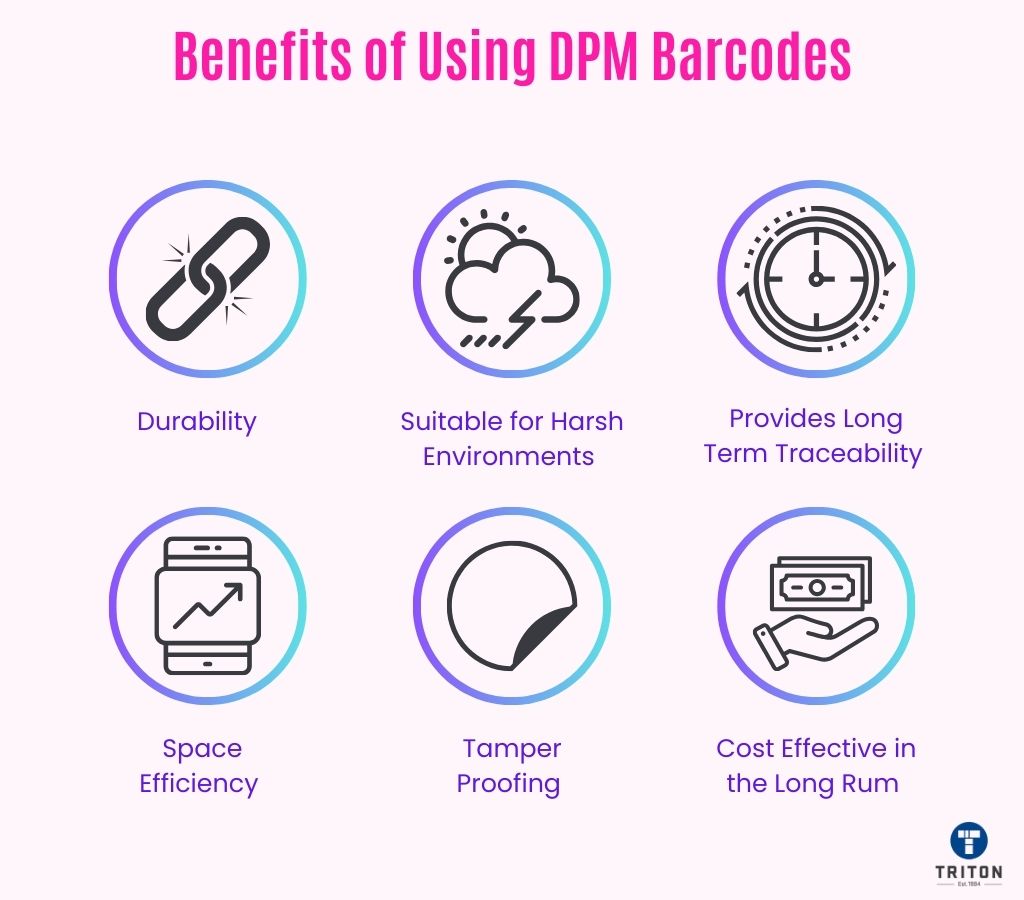
Using DPM barcodes offers several advantages, especially in contexts where durability and longevity are paramount. Below, we delve into the myriad of reasons why various industries and businesses are gravitating towards adopting DPM barcodes.
Durability
Since DPM barcodes are etched or imprinted directly onto the item, they are inherently more resistant to wear and tear. They don’t face common issues like peeling, smudging, or fading that can occur with traditional sticker labels.
Harsh Environment Suitability
DPM barcodes can withstand extreme conditions such as high temperatures, moisture, corrosive environments, and abrasive processes. This makes them ideal for industries like aerospace, automotive, and manufacturing, where items might be exposed to challenging environments.
Long-Term Traceability
DPM barcodes, by being directly etched onto items, ensure that the codes remain legible throughout the product’s lifecycle. This guarantees uninterrupted tracking and reliable traceability from the manufacturing stage to the end of the product’s utilisation, irrespective of time span or environmental wear.
Space Efficiency
DPM barcodes seamlessly integrate onto an item’s surface, proving advantageous in scenarios where space is at a premium or where attaching a label might be impractical or undesirable.
Tamper Proofing
As DPM barcodes are etched or imprinted directly onto the surface of the item, they minimise the risk of tampering with barcodes.
Cost-Effective in the Long Run
DPM streamlines inventory and logistics processes by ensuring that barcodes remain legible, mitigating operational disruptions and averting potential financial losses or unforeseen expenses.
Methods of Creating DPM Barcodes
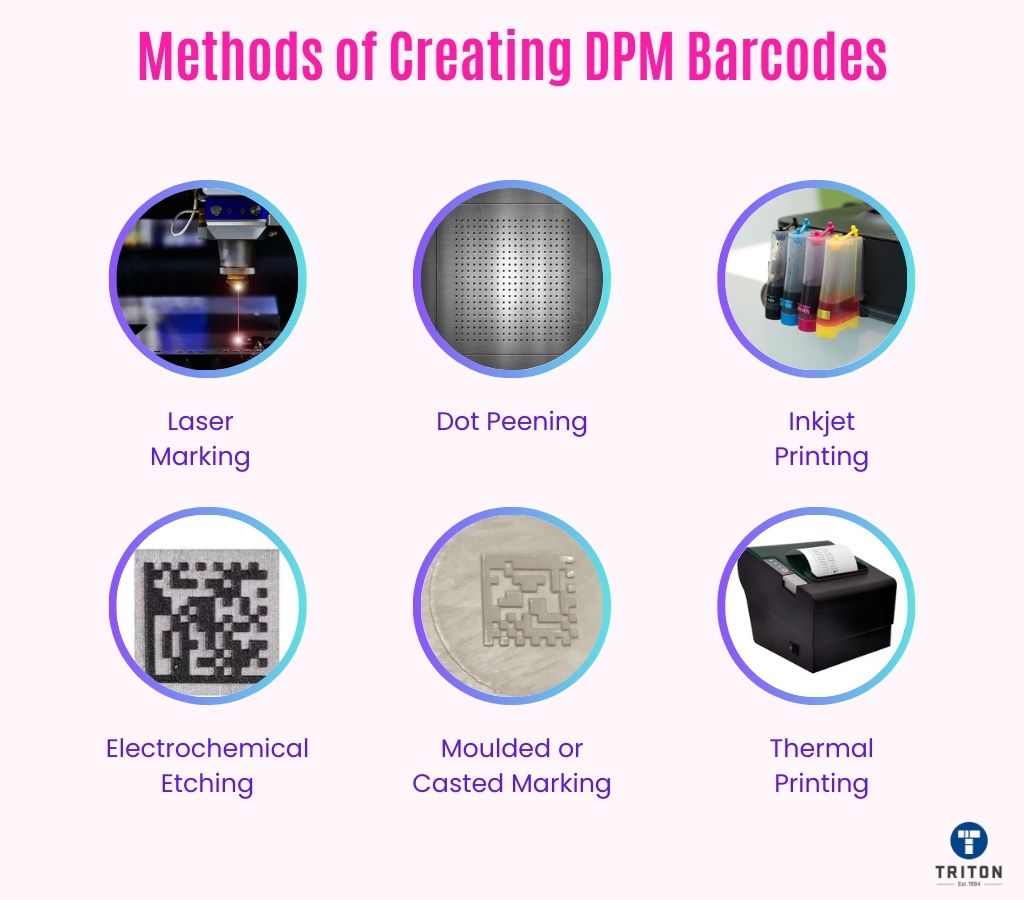
Direct Part Marking (DPM) barcodes are created using various methods, each suitable for different materials and application requirements. Here are the primary methods for creating DPM barcodes:
Laser Marking
Laser marking is one of the most prevalent methods for DPM technology. It involves using a laser beam to alter the material’s properties, resulting in a permanent mark.
- Advantages: High-quality marking, rapid productivity, and no need for consumables.
- Applications: Suitable for a wide range of materials, including metals, plastics, and ceramics.
Dot Peening
Dot peening uses mechanical percussion to create markings. It involves a stylus or pin that rapidly punches a series of dots into the material’s surface, forming the barcode pattern.
- Advantages: Durable and widely used for metals.
- Applications: Commonly used in the automotive industry for marking metal parts.
Inkjet Printing
Inkjet DPM barcodes are printed by spraying ink onto the surface to create the barcode. The ink is deposited in a pattern corresponding to the barcode design.
- Advantages: Versatile and can be used on various substrate materials.
- Applications: Suitable for materials like plastic, metal, glass, and more.
Electrochemical Etching
The electro-chemical etching method uses a stencil and an electrolyte solution in conjunction with an electric current to etch the barcode onto metal surfaces.
- Advantages: Produces a clear and durable mark without distorting the material.
- Applications: Used for marking metals, especially stainless steel.
Moulded or Casted Marking
In the moulded or casted marking technology, the barcode is integrated into the mould or cast used to form the part. When the material is moulded or cast, the barcode is formed as an integral part of the item.
- Advantages: Extremely durable as the barcode becomes an inherent part of the product.
- Applications: Suitable for plastic and metal parts that are moulded or cast.
Thermal Printing
Thermal printing uses heat to transfer a barcode design from a ribbon onto a material’s surface. Check out our dedicated guide on how thermal printers work to learn the science behind thermal print technology.
- Advantages: Quick and can produce high-resolution barcodes.
- Applications: Used for labels and tags that are then attached to products.
Thermal printing is of two types – Direct thermal and thermal transfer. Our guide on direct thermal vs thermal transfer explains and compares both thermal print technology types.
Triton is your comprehensive destination for all your thermal printing requirements. Our carefully curated collection showcases cutting-edge thermal printers sourced from industry giants such as Epson, Element, Senor, Honeywell, Zebra and TSC, along with a selection of coloured label printers from OKI.
Our inventory stocks a wide spectrum of thermal printers, including direct thermal printers, thermal transfer printers, barcode label printers, desktop printers, industrial printers, mobile printers and receipt printers.
Apart from thermal printers, we also offer premium thermal print consumables that adhere to the industry’s most stringent standards. Our offerings include a wide array of essential supplies, such as thermal transfer ribbons, thermal labels, thermal carton labels, thermal carcase tags, food-compliant thermal inserts, receipt rolls and shipping & freight labels.
With Triton, you’re not just investing in products; you’re investing in quality and performance. Beyond our product lineup, our unwavering commitment extends to providing exceptional customer support. Our dedicated team is a mere click away, accessible through our live chat widget below, and always ready to guide you in making informed purchasing decisions.
Types of Direct Part Marking Barcode Scanners
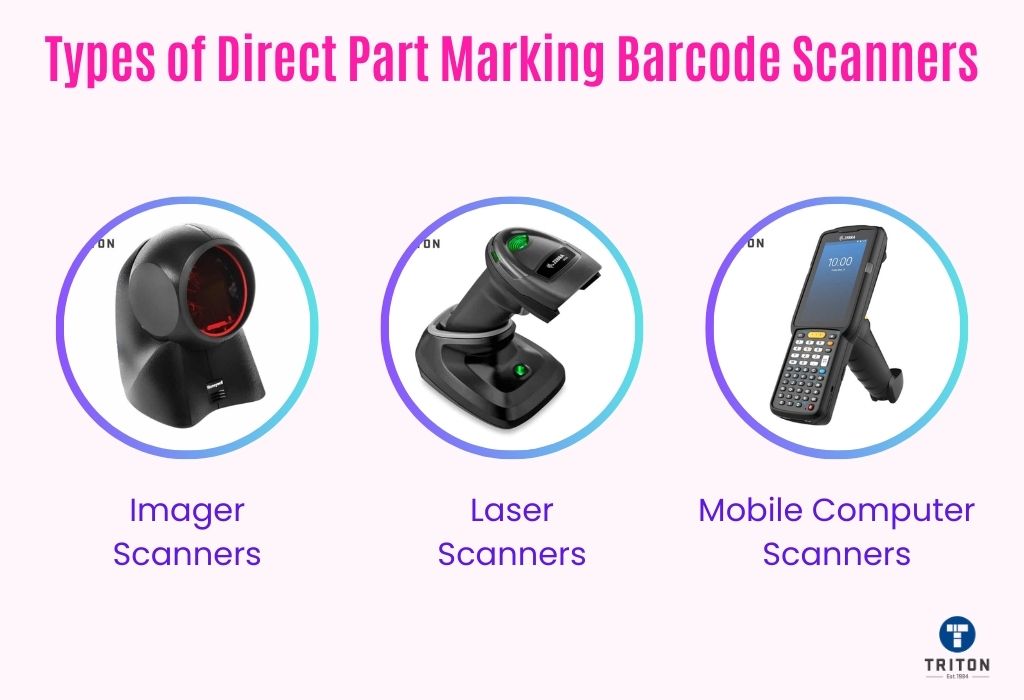
DPM barcodes, due to their unique marking methods and often challenging surfaces, require specialised barcode scanners. These are not your typical retail barcode scanners.
To gain a comprehensive understanding of how barcode scanners operate, we recommend referring to our guide on how do barcode scanners work.
Imager Scanners
These are the most common for DPM barcodes. They capture an image of the barcode, which is then processed and decoded. They can read both 1D and 2D barcodes.
Laser Scanners
Laser scanners read barcodes by shining a laser and measuring the light that bounces back.
Barcodes have dark and light areas. The dark areas absorb the laser, and the light areas reflect it. The scanner detects this reflected light to understand the barcode’s data.
With DPM barcodes, this can be a bit trickier since they’re etched directly on materials. These materials can sometimes interfere with the laser’s reflection, making reading more challenging.
In short, laser scanners use light reflection to read barcodes, but with DPM barcodes, the material’s nature can affect this reflection. They’re primarily used for 1D barcodes.
Mobile Computer Scanners
Mobile barcode scanners with built-in computing capabilities are a one-stop solution for on-the-go data management. They have the following benefits.
- Immediate Interpretation: Upon scanning a DPM barcode, these devices don’t just read; they understand, processing the data instantly.
- Data at Fingertips: They house internal storage, allowing users to access vital information immediately without needing external databases.
- Seamless Mobility: Lightweight and handheld, they support dynamic operations, enabling users to move freely, capturing and accessing data wherever needed.
At Triton, we get how vital barcode scanning is. That’s why we’re dedicated to providing our customers with top-notch barcode scanners from trusted brands like Honeywell and Zebra.
Our scanner range is pretty vast, making sure there’s a barcode scanner that suits any Aussie business. We’ve got USB barcode scanners, general barcode scanners, rugged barcode scanners, fixed scanners & sensors, 2D barcode scanners, mobile terminals, wireless barcode scanners and Bluetooth barcode scanners.
Why wait any longer? Shop with us and start scanning with ease. To learn more about our barcode scanning products, please contact us through the live chat widget below. We’re excited to help you find the perfect barcode scanning solutions for your needs, mate!
Common Industry Uses of DPM Barcodes
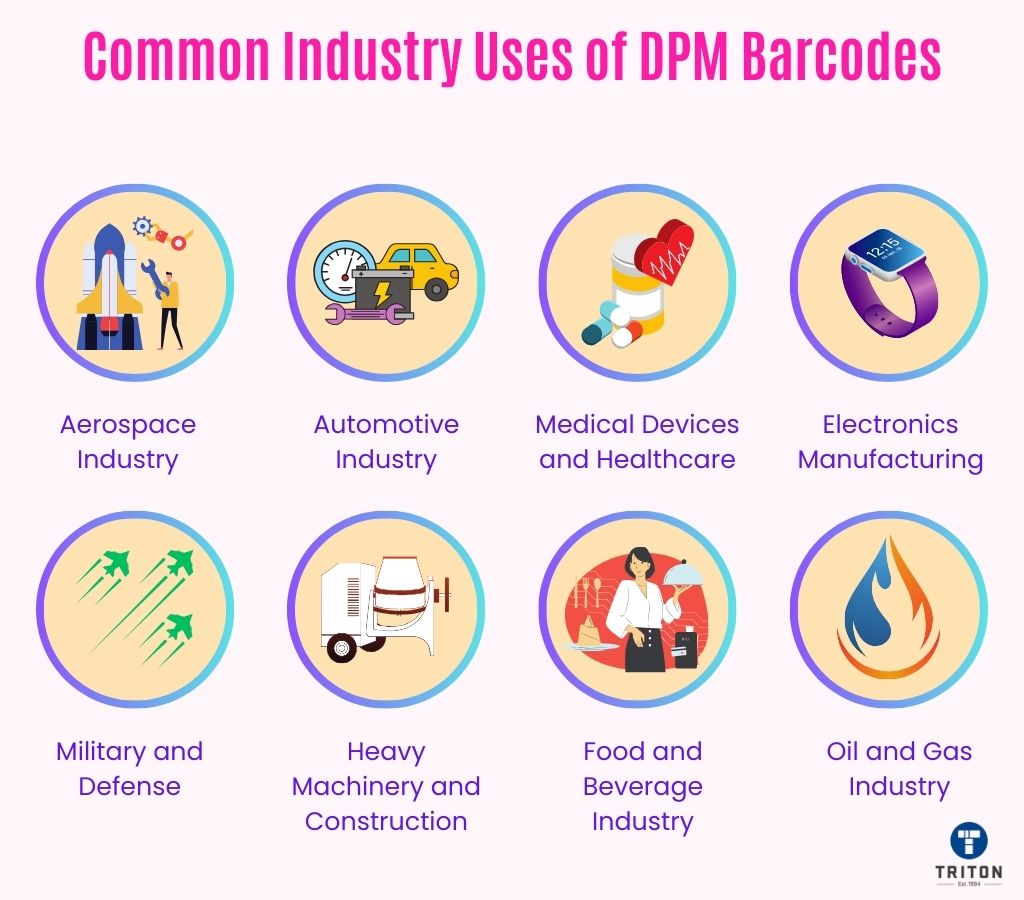
DPM barcodes are used in a variety of industries. The most common industries are discussed below.
Aerospace Industry
In the aerospace sector, DPM barcodes are pivotal in ensuring traceability and compliance with stringent regulations. Components like turbine blades, landing gear, and other critical parts are often marked with DPM barcodes to facilitate tracking throughout their entire life cycle, ensuring safety and aiding in maintenance and repair operations.
Automotive Industry
The automotive industry leverages DPM barcodes to manage and track parts throughout the manufacturing process and subsequent supply chain. From engine components to safety systems, DPM barcodes ensure each part can be traced back to its origin, aiding in quality control, recalls, and warranty services.
Medical Devices and Healthcare
In healthcare, DPM barcodes track and manage medical devices and surgical instruments, ensuring patient safety and compliance with regulatory requirements. Implants, surgical tools, and other critical devices are often marked to facilitate traceability, manage inventory, and ensure proper usage and maintenance.
The marking of such healthcare assets is extremely important. Our article on asset tagging will help you learn the importance of asset tagging.
Electronics Manufacturing
The electronics industry employs DPM barcodes to manage components and finished products, ensuring traceability and authenticity. From microchips to larger components, DPM barcodes help manage inventory, ensure quality control, and protect against counterfeit products.
Military and Defense
In the defence sector, DPM barcodes are utilised to manage assets and ensure the traceability of critical components. From weaponry to communication devices, DPM barcodes help maintain a secure and efficient supply chain, ensuring that each component can be accounted for and traced back to its source.
Oil and Gas Industry
The harsh environments of the oil and gas industry necessitate durable labelling solutions. DPM barcodes are used on drilling equipment, pipelines, and safety systems to ensure they can be effectively managed and maintained, even in corrosive and high-pressure environments.
Food and Beverage Industry
DPM barcodes are used in the food and beverage industry to track production equipment and manage assets. This ensures compliance with food safety regulations and helps in maintaining quality control throughout the production process.
Heavy Machinery and Construction
In the realm of heavy machinery and construction, DPM barcodes are employed to manage parts and equipment, ensuring they are properly maintained and safe to use. This aids in scheduling maintenance, managing recalls, and ensuring that machinery is compliant with safety regulations.
Challenges of Using DPM Barcodes
While DPM barcodes have revolutionised traceability and data storage across various sectors, it’s imperative to delve into the hurdles that organisations might face in their implementation and ongoing use.
Here are some challenges of using DPM barcodes.
Surface Variability
The diversity in materials, ranging from metals to plastics, and their inherent properties like surface texture, reflectivity, and colour can pose significant challenges in ensuring consistent and accurate barcode reading. Different materials might require varied marking techniques to ensure the barcode is legible and durable.
Wear and Tear
Despite being designed to endure throughout a product’s lifespan, DPM barcodes are not immune to the adversities of harsh conditions, such as extreme temperatures, chemical exposures, and physical abrasions. Over time, these factors can degrade the barcode, impeding its scannability and reliability.
Specialised Equipment and Lighting
Scanning DPM barcodes often necessitates specialised equipment due to the typically lower reflectance of the marked surface compared to traditional labels. Special lighting conditions are often required to accurately scan these barcodes, which might necessitate investment in advanced scanning technologies and devices.
Marking Consistency
Achieving a consistent and accurate mark, especially on uneven or textured surfaces, can be a formidable challenge. Inconsistent or imprecise markings can lead to scanning errors, impacting the reliability of data retrieval and potentially disrupting inventory and management systems.
Compliance and Standardisation
Ensuring that DPM barcodes comply with industry standards and international regulations is crucial. Different sectors, such as automotive, aerospace, and medical devices, have varied structuring for data encoded in barcodes, necessitating meticulous attention to detail in encoding and verification processes.
Cost Implications
The initial setup, including acquiring marking equipment and scanners capable of accurately reading DPM barcodes, can be capital-intensive. Additionally, training personnel to accurately create, manage, and scan DPM barcodes also involves additional costs and resource allocation.
Frequently Asked Questions
What Type Of Barcode Is Used for DPM?
Predominantly, 2D barcode symbologies like QR codes and Data Matrix codes are utilised for DPM codes owing to their error correction capabilities.
Do I Need Special Equipment to Read DPM Barcodes?
In most cases, standard barcode readers can decode DPM barcodes. However, specialised scanners might be required if the barcode is particularly small or on a challenging surface.
Are DPM Barcodes Different from Regular Barcodes in Appearance?
No, DPM barcodes are not different from regular barcodes in appearance.
The difference lies in how it’s applied. Instead of being printed on a label, a DPM barcode is etched or imprinted directly onto the item.
Is DPM Only for Industrial Use?
While DPM is popular in industries like aerospace, automotive, and healthcare due to its durability, it can be used wherever a permanent marking solution is beneficial.
Can DPM Barcodes Be Used on Various Materials?
Yes, DPM barcodes can be applied to a variety of materials, including metals, plastics, and ceramics, adapting to different industry needs.
Final Thoughts
Direct Part Marking barcodes stand out in the realm of product management and traceability. They offer a sturdy, lasting solution for embedding information directly onto items.
Throughout this article, we’ve explored the various facets and applications of DPM barcodes. Their use spans numerous industries, providing a resilient alternative to conventional labels. This is especially true in harsh or demanding environments.
Despite facing challenges like surface variability and wear, DPM barcodes (mostly QR code and Data Matrix code) are widely adopted. They play a crucial role in ensuring long-term traceability and compliance. They also efficiently manage items throughout their lifecycle.
As technology evolves, so will the methodologies and applications of DPM barcodes. Their relevance and utility will continue to weave into modern manufacturing and product management.
We hope this article was useful. Thanks for reading!